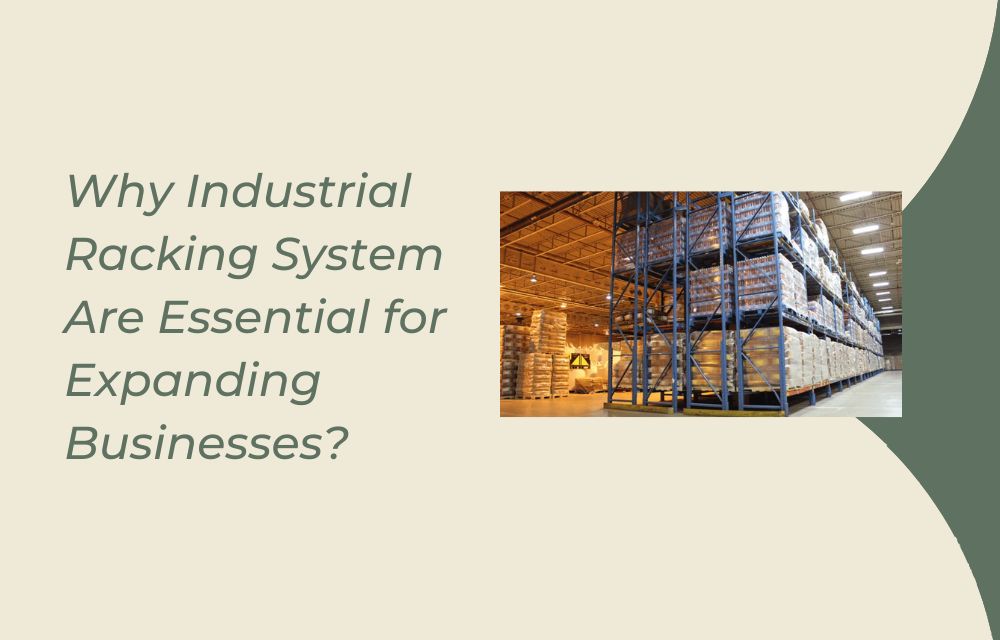
An industrial racking system is more than just a set of shelvesโit is a sophisticated storage solution designed to optimize space, improve workflow, and enhance operational efficiency. Whether you’re running a small warehouse or a large distribution center, industrial racking systems can significantly change the way your business operates.
In this article, weโll explain how industrial racking systems work, the various types available, and why they are considered game-changers for logistics and operations.
What is an Industrial Racking System?
The Basics of Industrial Racking Systems
An industrial racking system is a storage solution used to store goods in an organized and efficient manner. It typically consists of a framework of beams, shelves, and supports designed to hold inventory off the floor, making it easier to store and retrieve products. These systems are often found in warehouses, factories, and distribution centers, where large quantities of items need to be stored and easily accessed.
The main advantage of industrial racking is that it utilizes vertical space. Instead of storing goods directly on the floor, racking systems allow you to stack items in tiers, making the most of the height of your warehouse. This method creates more room for storage, ultimately leading to better space management and increased capacity.
Note:-ย In the UAE and looking for a dependable industrial racking system? For dependable, long-lasting racking solutions that are customized to your company’s requirements, get in contact with Stormat Systems. The knowledgeable staff will assist you in making the most of the space in your warehouse or facility, increasing efficiency, and optimizing storage. Get in touch with right now to find out more about ย industrial racking system in UAE and how we can help your company!
Types of Industrial Racking Systems
There are various types of racking systems, each designed to meet specific storage needs. Some of the most common types include:
-
Selective Racking: This is the most common type of racking system, where each pallet or item can be accessed directly. Itโs ideal for warehouses with a wide variety of items and provides easy access to individual products.
-
Drive-In Racking: This high-density system allows forklifts to drive into the rack to store or retrieve goods. Itโs designed for items that are often stored in bulk, reducing the number of aisles needed in a warehouse.
-
Push-Back Racking: This system allows products to be pushed back along rails, making it easy to store multiple items in a small area. The system is particularly useful for products that are stored in a first-in, last-out (FILO) order.
-
Cantilever Racking: Best suited for storing long, bulky, or irregularly shaped items like pipes, timber, and other large products. The open design makes it easy to store and retrieve long items.
-
Pallet Flow Racking: This system uses gravity to move products along inclined rollers, allowing pallets to flow from the back to the front of the system automatically. Itโs ideal for items that have a high turnover rate.
How Industrial Racking Systems Improve Logistics and Operations
1. Maximizing Storage Space
One of the primary reasons why industrial racking systems are considered a game-changer is their ability to maximize storage space. Traditional shelving can only utilize horizontal space, leading to wasted floor area. In contrast, racking systems make use of vertical space, stacking items several tiers high and increasing your overall storage capacity.
For example, using pallet racks can allow you to store goods higher up in the warehouse. This is especially important if your warehouse has a tall ceiling, as it makes better use of the height, creating more room for inventory without needing to expand your physical space.
By using high-density storage solutions such as push-back racking or drive-in racking, you can further optimize your available space, which helps you store more products without needing more warehouse square footage.
2. Improving Efficiency in Order Picking
Industrial racking systems significantly improve the order-picking process. When products are organized systematically on racks, itโs easier for warehouse workers to locate and retrieve them. This efficiency directly leads to faster order fulfillment times, which is essential in meeting customer demands.
In selective racking systems, items are placed in clearly marked sections, allowing for easy identification and quick access. In pallet flow racking or push-back racking systems, goods move automatically, which further improves picking times by reducing manual handling.
With the help of racking systems, warehouse workers can spend less time searching for products and more time preparing them for shipment. This streamlining of operations also reduces the likelihood of errors, improving accuracy in order fulfillment.
3. Enhancing Safety and Organization
Maintaining an organized warehouse is crucial not only for productivity but also for safety. Industrial racking systems are designed to keep products off the floor, reducing clutter and preventing items from being stacked haphazardly. This organization not only helps with space utilization but also reduces the risk of accidents in the warehouse.
For example, when goods are stored properly on racking systems, there is less chance of products falling, which could lead to injuries or damage. A well-organized warehouse also provides clear pathways for employees to move around safely without tripping over boxes or pallets.
Additionally, racking systems are often designed with safety features like secure shelving, proper weight distribution, and load-bearing limits to ensure that they can safely hold the products stored within them.
4. Increasing Inventory Control
Effective inventory control is essential for keeping a business running smoothly. Industrial racking systems play a major role in improving inventory management. With the organized layout provided by these systems, itโs easier to track product movement, monitor stock levels, and perform inventory counts.
Many modern racking systems can be integrated with warehouse management software (WMS) to track the movement of goods in real time. This integration improves inventory visibility and ensures that you have accurate information about stock levels. It also reduces the chances of overstocking or understocking items, which can result in lost sales or excess storage costs.
5. Reducing Labor Costs
Industrial racking systems can help reduce labor costs by improving workflow and reducing the amount of time workers spend on tasks like sorting, lifting, or carrying products. With a more efficient storage system, employees can quickly find what they need, reducing the time it takes to pick and pack orders.
Additionally, racking systems that allow for easy access to items or automate some of the storage and retrieval processes (such as pallet flow racking or drive-in racking) can reduce the need for manual labor, further cutting down on operational costs.
6. Flexibility and Scalability
As your business grows, your storage needs will change. Industrial racking systems are flexible and scalable, meaning they can be easily adjusted to accommodate new products or increased demand. Racking systems can be expanded, reconfigured, or moved to suit your evolving needs.
For example, if you find that youโre storing more bulky items, you can switch from a selective racking system to a cantilever racking system. Alternatively, if you need to store products more efficiently, you can transition to a push-back or pallet flow racking system.
This flexibility ensures that your racking system can grow with your business, allowing you to maximize your storage capacity at all times.
How to Choose the Right Industrial Racking System
1. Assess Your Storage Needs
Before selecting a racking system, take a close look at the types of products you need to store. Consider the size, weight, and turnover rate of your goods. Different types of racking systems are suited to different types of inventory, so choosing the right one for your products will help optimize your storage.
2. Consider Your Warehouse Layout
The layout of your warehouse will influence your choice of racking system. If you have limited aisle space, you may want to choose a narrow aisle racking system to maximize storage while maintaining safe access. If your warehouse has a high ceiling, a high-density racking system like drive-in racking can help you make the most of the vertical space.
3. Think About Future Growth
As your business grows, your storage needs will change. Choose a racking system that can be easily scaled up or reconfigured to meet future requirements. A system that can adapt to your evolving needs will provide better long-term value.
Conclusion
An industrial racking system is a crucial investment for businesses looking to improve the efficiency and organization of their logistics operations. These systems provide significant benefits, including maximizing storage space, improving order picking efficiency, enhancing safety, and reducing labor costs. By carefully selecting the right racking system for your business, you can improve your overall operational performance, reduce costs, and increase productivity.
Investing in the right racking system is more than just a storage solutionโitโs a game-changer for businesses looking to stay competitive in todayโs fast-paced logistics environment. Whether youโre looking to optimize a small warehouse or a large distribution center, industrial racking systems can make all the difference.
Note:- To read more articles visit on ideaepic.
Leave a Reply