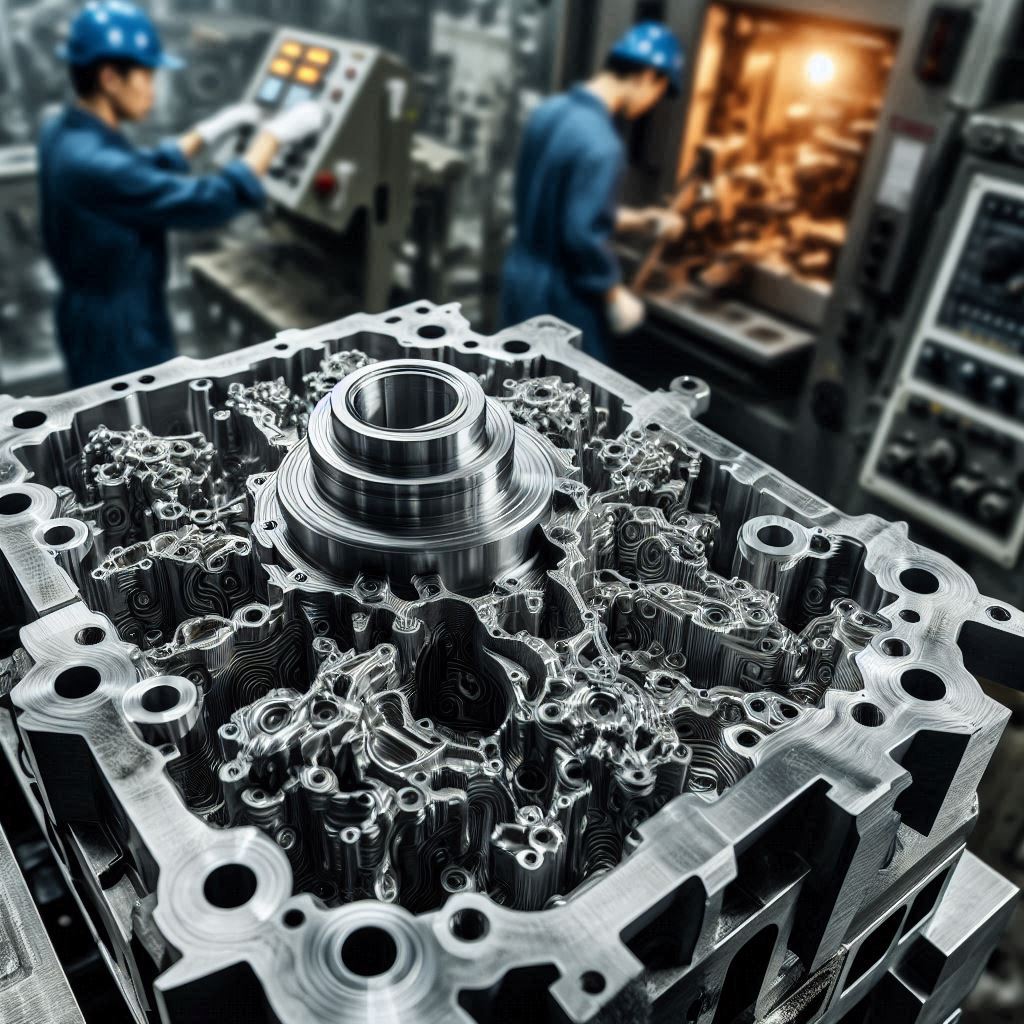
Machined investment casting is a very intricate manufacturing procedure for producing complex metal components at very high tolerances and with superior surface finishes. This is typically the most commonly used process for making high-performance components in many industrial applications such as aerospace, automotive, medical, and defense industries. Investment casting foundries establish quality control (QC) processes to monitor production stages strictly to achieve the highest of quality criteria. These activities identify defects, maintain dimensional fidelity, and guarantee material integrity.
Importance of Quality Control in Machined Investment Casting
Quality control in machined-in-castings is needed for the following:
- Compliance requirements of the industry for the parts.
- Prevention of all defects that would affect performance or safety.
- Efficiency increases by minimizing material wastage and rework.
- Reliability and durability of products.
Key Quality Control Steps in Machined Investment Casting
1. Raw Material Inspection
It begins with the use of high-quality raw materials such as stainless steel, aluminum, or superalloys. The compatibility is verified through spectroscopy and chemical analysis to ascertain material consistency with industry standards.
2. Wax Quality Checks
This is because any defect in it will lead to an error in the final casting as it is the direct representative of the final part. The quality checks comprise:
- Visual Inspection for Surface Defects
- Dimensional Verification Using Gauges and Measurement Tools
- X-ray or ultrasonic testing to detect internal inconsistencies in wax patterns
3. Ceramic Shell Inspection
This the mold or the hollow shell for the molten metal. It must not contain cracks, irregularities, or air pockets as it will influence the integrity of the casting process. The foundries conduct:
- Visual and microscopic inspection of the shell.
- Strength and permeability tests in order to ascertain durability when metallic pouring is done.
4. Metal Pouring and Solidification Monitoring
Controlled pouring techniques, such as vacuum or gravity pouring, are used to prevent air entrapment and oxidation. Checks during this stage include:
- Monitoring the temperature of molten metals to ensure fluidity.
- Solidification analysis helps to avoid shrinkage defects and porosity.
- Confirming alloy composition through spectrographic testing.
5. Post-Casting Inspections
As soon as the casting solidifies and the ceramic shell is removed, foundries conduct the following inspections:
- Visual Inspection- Checking for external defects such as cracks, voids, or rough surfaces.
- Non-Destructive Testing (NDT)- X-ray, ultrasonic, or dye penetrant testing to detect internal flaws.
- Hardness and Tensile Testing- Ensuring mechanical properties meet specifications.
Summary
The process of quality assurance in investment casting does not end with machining; it is done so comprehensively and at various stages to ensure the components are characterized by exactitude, durability, and reliability. However, rigorous inspection and testing facilitate the delivery of excellent performance parts, compliant with the increasingly demanding needs of today’s industries. As such, investment casting foundries are indeed perfecting their quality inspection processes, whether through automation, digital inspection, or AI-driven quality analytics, to achieve greater accuracy and efficiency.
Leave a Reply