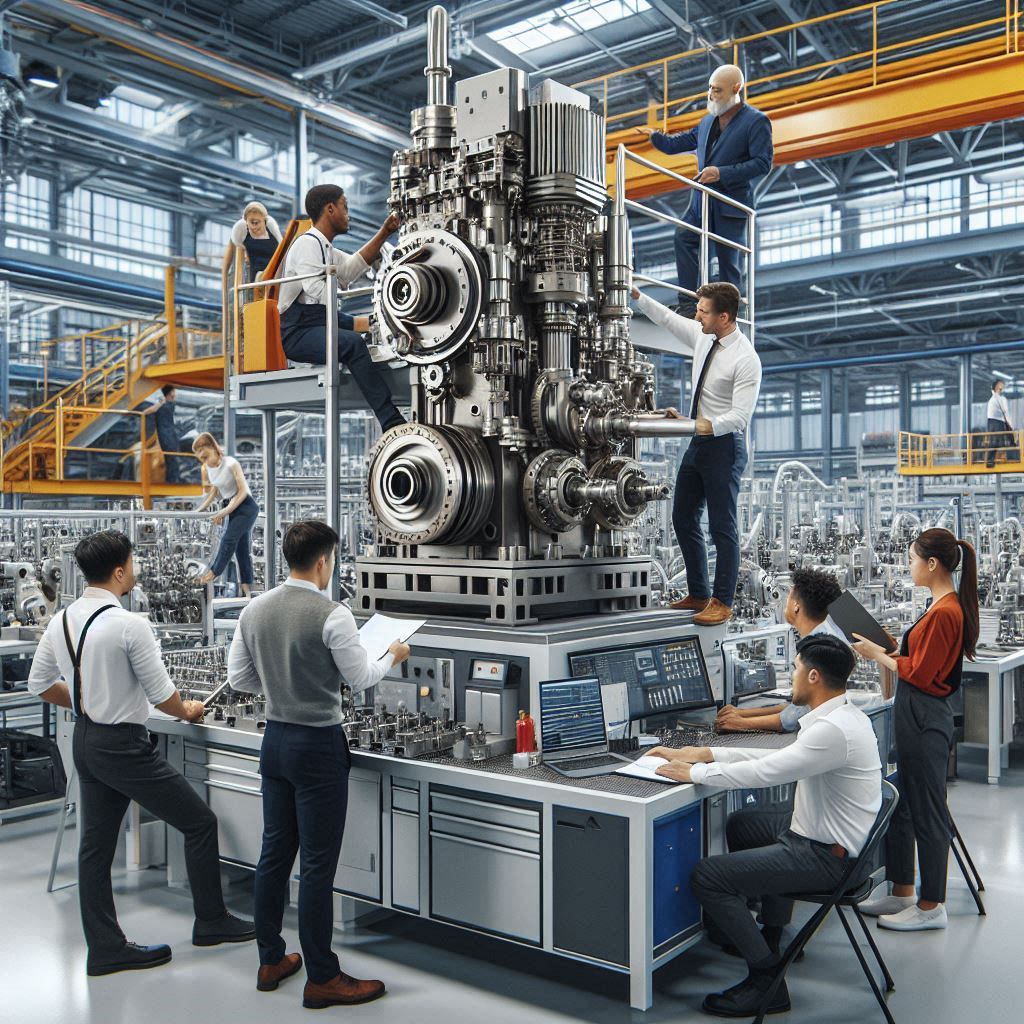
Pump casting is heart in the process that once determines the pumps to be manufactured in different industries like oil and gas, chemical processing, water treatment, and electricity generation. The durability and quality of any pump are directly dependent on the role pump casting manufacturers play in making it. All pump casting manufacturers thus have the responsibility on working to make sure that pumps operate in highly efficient conditions and let high pressures, temperatures, and corrosive environments act upon them for a long time.
Understanding Pump Casting
In pump casting, the forming of metal pump components such as casings, impellers, and volutes occurs via a cast method. An important parameter is the dimension because it helps to let the fluid through with the minimum amount of resistance and energy loss. The material for making pump casting can be cast iron, stainless steel, bronze, and other high-strength alloys depending on the application.
The techniques used of pump casting manufacturers are the following:
- Sand casting – best for very large and complicated setups of pumps components.
- Investment casting – High-finish quality and dimensional precision.
- Die casting – The die casting process is usually used for mass production and high uniformity.
Key Roles of Pump Casting Manufacturers
1. High Quality Manufacturing
Pump casting manufacturers set high quality controls for manufacturing components that must survive to serve. They thus use advanced casting processes and precision machining and put these components through rigorous tests to ensure conformity to standards: ASTM, ANSI, ISO, and others. Among the services that may be included are:
- Material composition analysis
- Dimensional Accuracy checks
- Pressure and leakage tests
- Corrosion and Wear resistance test
2. Customization for Industry-Specific Applications
Different industries require pumps with distinct characteristics to resist high temperatures or corrosive chemicals, even high pressures. Hence, Β Pump casting manufacturer work with the client to customize the solution that addresses those operational requirements.
For example:
- The Oil and Gas Industry: Needs pumps that have high pressures and corrosion resistance.
- Chemical Processing: Pumps need to withstand acidic and alkaline liquids.
- Water Treatment: Durable pumps, efficiently running to carry on with continuous usage.
3. Innovations in Material and Design
With the latest technological upgrade, much of the development in the design and material is meant to address the efficiency and lifespan of components. Modern techniques of manufacturing such as computer-aided design (CAD), 3D printing, etc., come into use to design new kinds of pump components to produce better working performance and energy efficiency.
4. Paving the Way for Industrial Growth and Infrastructure
Pump casting manufacturers is the direct and indirect support to industrial operations through supplying functional components for different fluid handling systems. These deal with fluid movement across the industries uninterruptedly and contribute further to the uninterrupted running of industries, thereby helping to decrease downtime and improve efficiency.
5. Sustainability and Eco-Friendly Practices
Understood as the industry trend in sustainability, pump casting manufacturers are imbibed within these practices such as:
- Metal waste recycling
- Energy-efficient alternatives for production
- Lightweight and energy-efficient components of pumps
Β
Conclusion
Pump casting manufacturers are active in manufacture quality, durability, and highly efficient pump components that work as motor to any industrial operation. Their knowledge about materials, precision casting technologies, and even innovative concepts will render reliable pumps to industries for different applications. Manufacturers are also beginning to adopt their processes toward sustainability and energy efficiency as technology progresses. Hence, it becomes so critical to choose the perfect pump casting manufacturer for the long-lasting performance and reliability of industrial applications.
Leave a Reply