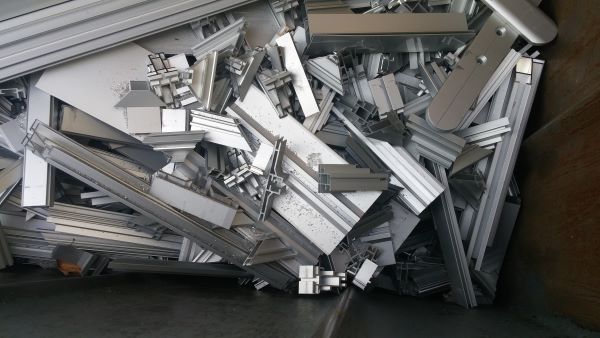
Aluminum is one of the most widely used metals in the world, prized for its lightweight, durability, and recyclability. As industries continue to evolve, the demand for aluminum raw materials has grown significantly, driven by sectors such as automotive, aerospace, construction, and packaging. This article explores the latest trends in aluminum raw materials, focusing on advancements in extraction, recycling, sustainability, and market dynamics.
1. Sustainable Sourcing and Green Aluminum
The Rise of Green Aluminum
One of the most significant trends in the aluminum industry is the shift toward sustainable sourcing and the production of “green aluminum.” Green aluminum refers to wholesale aluminum metal raw material supplier produced using renewable energy sources, such as hydroelectric, solar, or wind power, rather than fossil fuels. This reduces the carbon footprint of aluminum production, which is traditionally energy-intensive.
Certification and Transparency
Companies are increasingly adopting certifications like the Aluminum Stewardship Initiative (ASI) to ensure responsible sourcing and production practices. Consumers and manufacturers are demanding greater transparency in the supply chain, pushing producers to disclose the environmental impact of their operations.
Impact on Market Dynamics
The demand for green aluminum is reshaping market dynamics, with premium pricing for low-carbon aluminum. This trend is particularly evident in Europe and North America, where environmental regulations are stricter, and consumers are more environmentally conscious.
2. Advancements in Aluminum Extraction Technologies
Improved Bauxite Mining Techniques
Bauxite is the primary raw material for aluminum production. Recent advancements in mining technologies have focused on reducing the environmental impact of bauxite extraction. Techniques such as precision mining and land rehabilitation are being employed to minimize deforestation and soil erosion.
Energy-Efficient Smelting Processes
The smelting process, which converts alumina into aluminum, is highly energy-intensive. Innovations such as inert anode technology and the use of renewable energy in smelters are reducing energy consumption and greenhouse gas emissions. Inert anodes, for example, eliminate carbon dioxide emissions during smelting, making the process more environmentally friendly.
Hydrometallurgical Methods
Researchers are exploring hydrometallurgical methods as an alternative to traditional smelting. These methods use chemical processes to extract aluminum from ores, potentially reducing energy consumption and emissions. While still in the experimental stage, these technologies could revolutionize aluminum production in the future.
3. Recycling and Circular Economy
Growing Emphasis on Recycling
Recycling is a cornerstone of the aluminum industry, as aluminum can be recycled indefinitely without losing its properties. The latest trend is the increased focus on creating a circular economy for aluminum, where end-of-life products are collected, processed, and reused in new applications.
Innovations in Recycling Technologies
Advanced sorting and separation technologies, such as AI-driven systems and eddy current separators, are improving the efficiency of aluminum recycling. These technologies enable the recovery of high-quality aluminum from complex waste streams, such as electronic waste and mixed materials.
Closed-Loop Recycling in Automotive and Packaging
The automotive and packaging industries are leading the way in closed-loop recycling. Automakers are using recycled aluminum to produce lightweight components, reducing vehicle weight and improving fuel efficiency. Similarly, beverage companies are incorporating recycled aluminum into cans, reducing the need for virgin materials.
4. Lightweighting and High-Strength Alloys
Demand for Lightweight Materials
The push for lightweighting in industries such as automotive and aerospace is driving demand for advanced aluminum alloys. Lightweight materials are essential for improving fuel efficiency, reducing emissions, and enhancing performance.
Development of High-Strength Alloys
Researchers are developing high-strength aluminum alloys with improved mechanical properties, such as increased tensile strength and corrosion resistance. These alloys are being used in critical applications, including aircraft structures, electric vehicle (EV) batteries, and renewable energy systems.
Aluminum in Electric Vehicles
The rise of electric vehicles (EVs) has created new opportunities for aluminum raw materials. Aluminum is used extensively in EV components, including battery enclosures, chassis, and body panels, due to its lightweight and thermal conductivity properties.
5. Geopolitical and Market Trends
Supply Chain Disruptions
The aluminum industry has faced significant supply chain disruptions in recent years, driven by geopolitical tensions, trade restrictions, and the COVID-19 pandemic. These disruptions have highlighted the need for diversified supply chains and strategic stockpiling of raw materials.
China’s Dominance in Aluminum Production
China remains the largest producer and consumer of aluminum, accounting for over half of global production. However, concerns over environmental regulations and energy consumption in China are prompting other countries to invest in domestic aluminum production capabilities.
Tariffs and Trade Policies
Trade policies, such as tariffs on aluminum imports, are influencing global market dynamics. For example, the U.S. imposition of tariffs on aluminum imports has led to increased domestic production and investment in recycling infrastructure.
6. Environmental and Regulatory Pressures
Stricter Environmental Regulations
Governments worldwide are implementing stricter environmental regulations to reduce carbon emissions and promote sustainable practices. These regulations are pushing aluminum producers to adopt cleaner technologies and reduce their environmental footprint.
Carbon Pricing and Emission Trading
Carbon pricing mechanisms, such as emission trading systems (ETS), are becoming more prevalent. These systems incentivize companies to reduce their carbon emissions by putting a price on carbon dioxide emissions. Aluminum producers are investing in carbon capture and storage (CCS) technologies to comply with these regulations.
Water and Energy Conservation
Water and energy conservation are critical focus areas for the aluminum industry. Innovations in water recycling and energy-efficient processes are helping producers reduce their resource consumption and operational costs.
7. Emerging Applications for Aluminum
Aluminum in Renewable Energy
Aluminum is playing a crucial role in the renewable energy sector. It is used in solar panels, wind turbines, and energy storage systems due to its lightweight and corrosion-resistant properties. The growing demand for renewable energy is expected to drive further growth in aluminum consumption.
Aluminum in 3D Printing
Additive manufacturing, or 3D printing, is emerging as a new application for aluminum. Aluminum powders are being used to produce complex components with high precision and reduced material waste. This technology is gaining traction in industries such as aerospace, healthcare, and automotive.
Smart Packaging Solutions
The packaging industry is exploring innovative uses of aluminum, such as smart packaging with embedded sensors. These solutions enhance product safety, extend shelf life, and provide real-time information to consumers.
8. Challenges and Future Outlook
Balancing Demand and Sustainability
One of the biggest challenges facing the aluminum industry is balancing growing demand with sustainability goals. Producers must invest in cleaner technologies and sustainable practices while meeting the needs of a rapidly expanding market.
Technological Innovation
Continued technological innovation will be essential for the future of aluminum raw materials. Advances in extraction, recycling, and alloy development will drive the industry forward and open up new opportunities.
Collaboration Across the Supply Chain
Collaboration across the supply chain, from miners to manufacturers, will be critical to achieving sustainability and efficiency goals. Partnerships and knowledge-sharing initiatives will help address common challenges and drive progress.
Conclusion
The aluminum industry is undergoing a transformative period, driven by sustainability, technological innovation, and changing market dynamics. From green aluminum and advanced recycling techniques to high-strength alloys and emerging applications, the latest trends in aluminum raw materials are shaping the future of this vital industry. As demand for aluminum continues to grow, stakeholders must work together to ensure a sustainable and resilient supply chain that meets the needs of a rapidly evolving world.
Leave a Reply