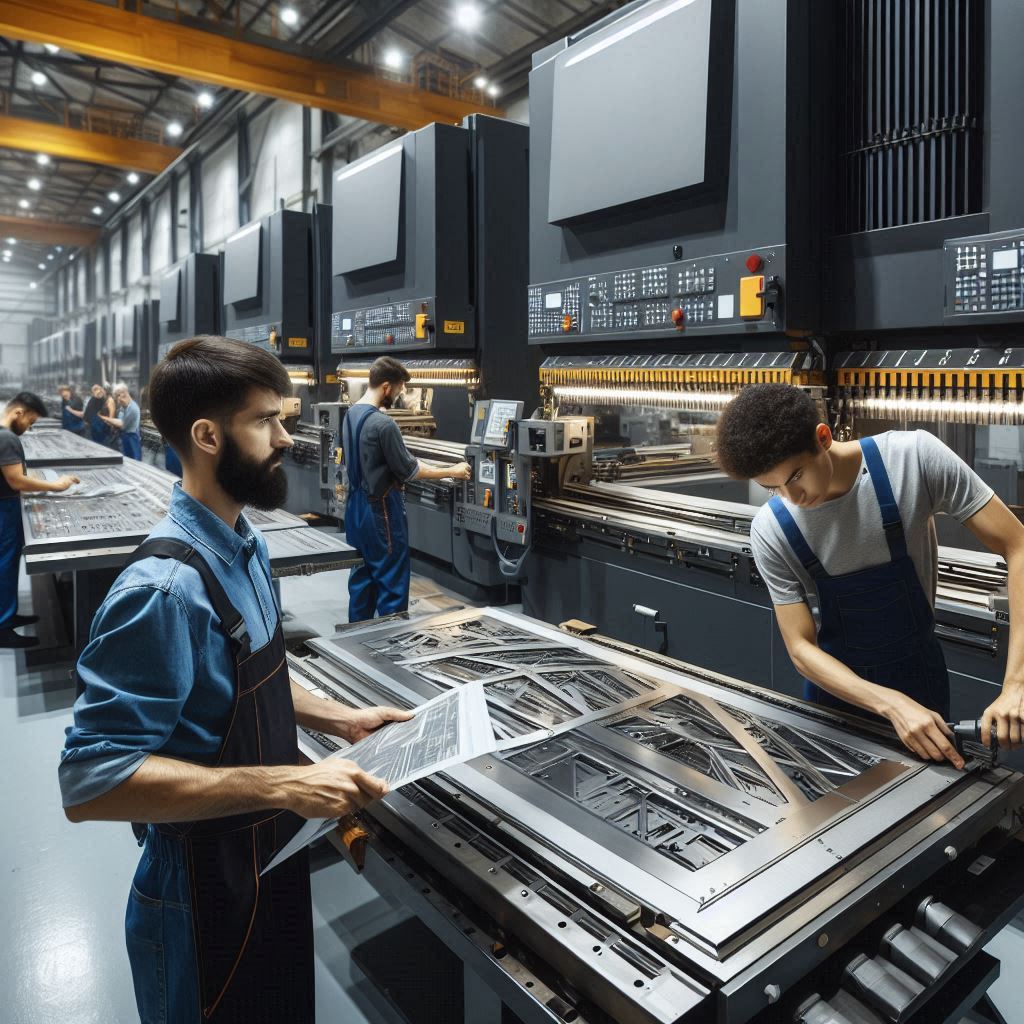
Manufactured products must now fulfil the rigorous requirements for precision and quality in order to become products that can be regarded as high-quality and reliable. They indeed keep boosting the requirements of the process for accuracy, efficiency, and consistency; while advanced manufacturing technologies would evolve, one such technology that has changed the industry of metal has become CNC (Computer Numerical Control) machines. Such advanced machines are transforming how one could bend metals as they can achieve unprecedented precision and control. This article would discuss the impact of CNC press brake machines on precision and quality control in metal fabrication.
Getting to Know CNC Press Brakes
A press brake is a part of machinery that bends and forms a metal sheet to a certain angle or shape using punch and die systems by applying certain amounts of force. A CNC press brake machine is a fully automated model under the use of computer programming to help control the bending process. Unlike traditional press brakes that require human operation, as well as all the required adjustments, CNC press brakes perform rather complex bending operations while requiring very little human involvement.
Within the computerized interface of the machine, operators can input specific measurements, angles, and dimensions pertaining to each bend they will make. Certainly, this would guarantee accuracy, so that each part would thus be bent in accordance with exact specification; it has made these machines increasingly utilized in high precision required industries like aerospace, automotive, and electronics.
Precision in Bending Operations.
One of the most distinct advantages of a CNC press-brake machine is that it enables precision accuracy, maximum in metal bending. In traditional press brakes, bending often depends on the skill and experience of the operator, leading to variations in the final product. Many causes of human error, inconsistency of force while applying pressure, and unable with some other measurement problem would altogether degrade the quality in bends.
CNC press brakes do away with all such issues, however, following precise instructions from a computer. Powered, speed, and positioning of the punch and die are all adjusted automatically to ensure that the metal will bend to the actual angle and shape required. Thus, that kind of precision not only reduces errors but also makes production more consistent with tight tolerances, which would be hard or even impossible to achieve with manual machines.
Increased Repeatability and Consistency
Apart from that, they ensure that a CNC press brake can repeatedly manufacture the same part with precisely the same measurement and identical bends. After putting the design and parameters into the CNC system, it can produce hundreds or thousands of identical items without variations. This is what makes it important because parts have to fit perfectly in some industries or need to meet strict standards for quality.
Furthermore, automated tool-setting systems complement that totally to the repro-dependability of CNC press brakes. Entirely automated tool setting reduces the chance of human error occurring during this process. The computer control for the machine guarantees that every time the tooling be applied, it would give consistent bending and improve overall quality.
Quality Control-Improved Waste Reduction
From matters concerning quality control to the manufacturing process, CNC press brake machines are very instrumental in ensuring that parts comply with required specifications. Automated bending can even allow monitoring and control by operators during processing, making it easy to know when something potentially problematic crops up.
For example, the CNC system would note any differences between this parameters for different material thicknesses or misalignment, which in turn influences adjustment of required pressure from connections for perfect bend. Moreover, in general, CNC press brakes can be equipped with integrated sensors that measure the angle and position of the bends while the machine operates, and should the machine find any deviation between the actual specification and the specified one, it might correct automatically the fault to prevent defects.
Moreover, CNC machines being that precise add to reducing the chance of error parts, affecting the waste as it causes fewer errors to process faulty parts through scrapping or reworking, unlike all such costs incurred directly or indirectly.
Data Logging and Real-Time Monitoring
Modern CNC press brake machines come with advanced software that gives information about bending processes in real-time. The software collects information about bend angles, forces applied, and properties of the material throughout the operation. Such data are accumulated at CNC press brake machine manufacturer to create detailed reports on machine conditions and output quality.
This is data-driven quality control that helps identify trends so that procedures can be optimized, while also allowing for predictive maintenance before a problem arises. It also acts as important documentation quality assurance for companies that demand it in industrial standards and certifications for their products.
Increased Operator Efficiency
While CNC press brake machines see exceptional improvements in the realm of precision and quality control, this machine has also made life easier for the operator. The great majority of the bend process is automated, so the operator does not have to make continuous manual changes or setup to make a part. Instead, the operator observes the operation and addresses any problems that arise.
Most CNC press brake machines provide easy-to-learn and operate intuitive interfaces as well. With minimal training, operators can input all the parameters required, reducing setup time, thus improving overall flow efficiency. Therefore, better precision and control quality have been engineered alongside improved productivity from quicker turnaround times.
Leave a Reply