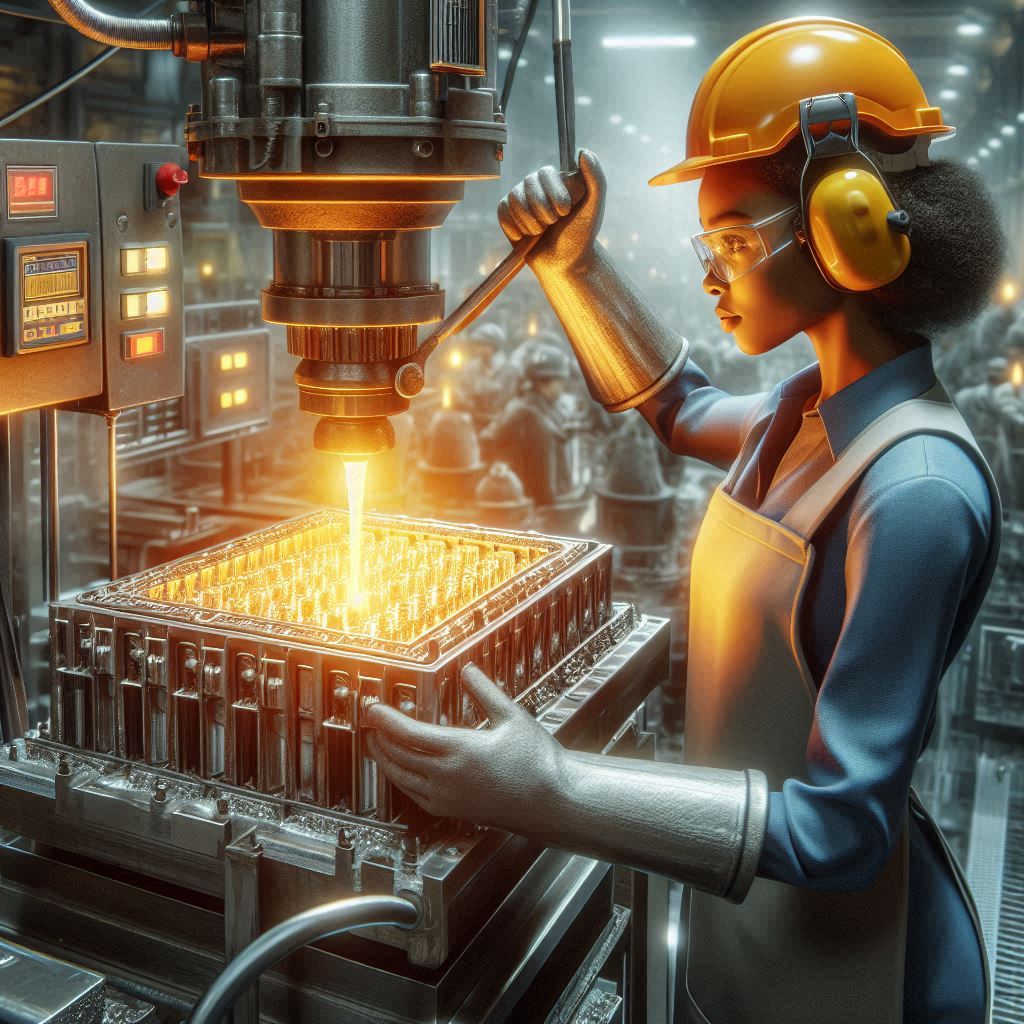
Precision investment casting or lost-wax method involves extremely high-precision manufacturing of complex or intricate metal components under tight tolerances. A wax pattern of the part desired is created and then a thin layer of ceramic is applied onto the surface followed by the removal of the wax through melting and draining as a result of which mold arises ready to be filled with molten metal. It allows parts to be produced with exceptional surface finish and complex geometries with the least amount of post-processing; and makes it an ideal process in precision-demanding fields such as aerospace, automotive and medical.
Precision investment casting would be learning about the manufacturing process.
The manufacturing methodology of precision investment castings, commonly labeled the lost wax methodology, is usually a very painstaking and multi-hued process that aims for nothing short of creating extremely precisely cast metal parts. The making of a wax pattern that is an exact replica of the desired part is the first step in the process followed by lnvestment. This wax pattern is then invested with a ceramic shell to create a mold. After the ceramic shell has been hardened, the molten wax is drained away, thereby leaving behind a hollow mold. This hollow mold is then heated, and molten metal is poured into it to fill the cavity and take the pattern of the original wax pattern. After cooling and solidification, the mold is broken off, and the cast part is highly finished, usually with very little machining. This process offers complex shapes with tight tolerances, having smooth surfaces, and with minimum materiais wastage; it therefore fits industries that very much desire accuracy and quality.
Methods of ensuring precision in Precision investment casting casting jobs by the manufacturers
Precision investment casting manufacturers enforce strict protocols to ensure precision during casting work, and most require high-tech processes, controls for quality, and manual dexterities. They first use high-end CAD/CAM to arrive at deviations that meet the desired pattern and prototyping specifications in the first instance. Next, injection molding achieves the most delicate detail on wax patterns, and several coats of ceramics are applied to create a mold strong enough to hold tight tolerances. The pouring process is done with great care and thorough controls on temperature and flow. Catered with these, such conditions guarantee most united casting. After casting, dimensions are inspected very carefully along their finish quality, usually with very sophisticated instruments such as CMMS (Coordinate Measuring Machines) for the measurement. By constant monitoring at every stage-from design to dispatch-manufacturers capture castings that very high in accuracy and reliability concerning the harsh industry requirements that exist today.
Leave a Reply