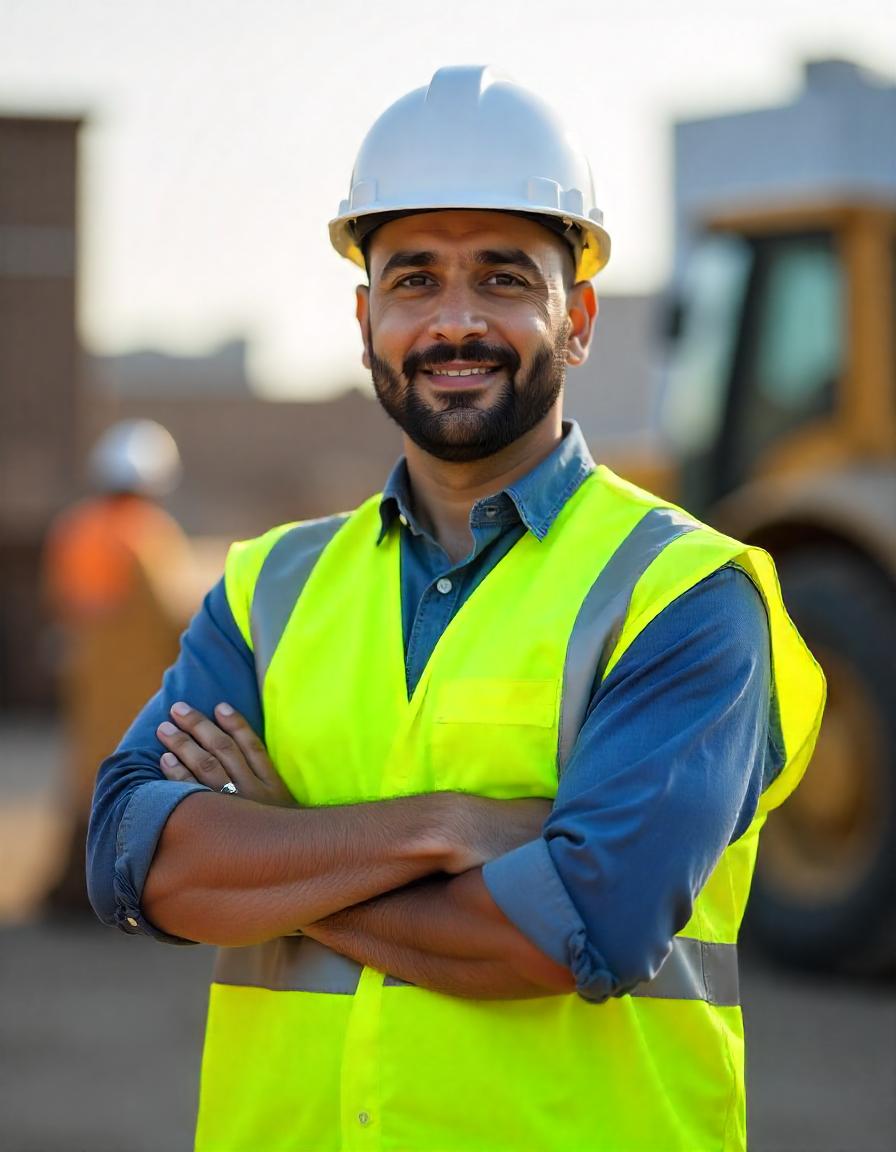
Airborne hazards are one of the most significant risks faced by workers across various industries, from construction to healthcare. These hazards can include dust, fumes, vapors, and other particles that can be harmful when inhaled. Understanding the guidelines set by the Occupational Safety and Health Administration (OSHA) is critical for employers and employees alike. This article provides an in-depth look at how OSHA guidelines help reduce airborne hazards in the workplace. Whether you are considering taking an OSHA Certificate or aiming for an OSHA 30 Hour Certification, knowing these guidelines will help ensure a safer working environment.
1. Introduction to OSHA Guidelines for Airborne Hazards
Airborne hazards in the workplace pose a significant risk to employee health and safety. Exposure to harmful airborne substances can lead to various respiratory problems, long-term diseases, and even death in extreme cases. OSHA, a federal agency dedicated to enforcing workplace safety, has set forth a series of regulations aimed at minimizing these risks. These regulations are designed to protect workers in industries that handle hazardous materials, dust, vapors, or fumes. By obtaining an OSHA Certificate, employees gain essential knowledge about these hazards and how to manage them effectively.
An OSHA 30 Hour Certification provides further expertise, especially for those in supervisory roles, ensuring that they can lead their teams with safety in mind. Whether you’re an employer looking to comply with safety regulations or a worker aiming to enhance your knowledge, these certifications are vital for reducing airborne hazards.
2. OSHAβs Role in Protecting Workers from Airborne Hazards
2.1 The Importance of Airborne Hazard Regulations
OSHAβs role is to ensure that employers provide safe and healthy working environments. For airborne hazards, OSHA guidelines help to limit the exposure of workers to dangerous substances by setting permissible exposure limits (PELs). These limits are based on a substanceβs toxicity and its potential to cause harm. Employers are required to monitor the air quality in workplaces, make necessary adjustments to ventilation, and implement other safety measures to ensure that airborne hazards are reduced to acceptable levels.
2.2 Standards Set by OSHA for Airborne Hazards
The OSHA regulations for airborne hazards cover a broad range of substances. These include asbestos, silica dust, welding fumes, lead, and more. The OSHA guidelines recommend using engineering controls, administrative controls, and personal protective equipment (PPE) to mitigate these risks.
- Engineering Controls: These include systems such as proper ventilation and air filtration that help prevent the accumulation of harmful airborne particles in the workplace.
- Administrative Controls: These controls involve altering work practices or shifting work schedules to limit exposure.
- Personal Protective Equipment (PPE): PPE includes respirators and other devices that protect workers from inhaling hazardous substances.
3. Effective Measures for Reducing Airborne Hazards
3.1 Air Quality Monitoring
One of the first steps in reducing airborne hazards is conducting regular air quality assessments. Employers should utilize OSHA-approved monitoring equipment to check for harmful concentrations of substances. Depending on the industry, this may involve measuring levels of dust, fumes, or gases.
By earning an OSHA Certificate, workers can become proficient in recognizing when air quality issues arise and learn how to respond. Regular air monitoring not only helps in ensuring compliance with OSHA regulations but also provides valuable data for making adjustments that improve workplace safety.
3.2 Proper Ventilation Systems
Good ventilation is crucial to reducing airborne hazards. Proper ventilation systems can help remove hazardous airborne substances and maintain air quality at acceptable levels. Employers are encouraged to install local exhaust systems or make modifications to their ventilation systems based on the nature of the airborne hazards present.
If you are working toward your OSHA 30 Hour Certification, you will learn how to design and maintain ventilation systems that comply with OSHAβs guidelines. Adequate ventilation can significantly reduce the need for personal protective equipment and make workplaces safer.
3.3 Use of Personal Protective Equipment (PPE)
When engineering and administrative controls are not enough to reduce airborne hazards, PPE becomes essential. Respirators are one of the most commonly used types of PPE for protecting workers from inhaling harmful airborne substances. However, selecting the right type of respirator depends on the type of hazard.
Training on the proper use of PPE, including respirators, is covered in the OSHA Certificate programs. It is critical to understand how to select, maintain, and use PPE to ensure maximum protection.
3.4 Employee Training and Education
Educating employees about the risks associated with airborne hazards and the proper safety measures is vital. OSHA requires employers to train workers on how to recognize and respond to hazards effectively. Training sessions often focus on proper ventilation, the use of PPE, and the significance of regular air quality monitoring.
The OSHA 30 Hour Certification provides in-depth training that goes beyond the basics, focusing on developing safety management skills and ensuring workers can handle complex air quality issues in large organizations.
4. Guidelines for Specific Airborne Hazards
4.1 Silica Dust
Silica dust, commonly found in construction and mining, is one of the most dangerous airborne hazards. Inhalation of silica dust can lead to serious health conditions, including lung disease and cancer. OSHA has set strict regulations for silica exposure, including the use of water sprays or ventilation systems to control dust levels.
Training in handling silica dust is included in OSHA 30 Hour Certification programs, equipping workers and supervisors with the necessary skills to implement effective controls.
4.2 Asbestos
Asbestos exposure remains a significant concern, particularly in older buildings. Asbestos fibers are highly dangerous when airborne and can lead to serious diseases such as mesothelioma. OSHA regulations require that employers protect workers from asbestos exposure by implementing strict air monitoring and control measures.
Through an OSHA Certificate, workers can learn how to manage and reduce exposure to asbestos in the workplace, ensuring that the appropriate safety measures are in place.
4.3 Welding Fumes
Welding operations often release harmful fumes that contain various metals and chemicals. Prolonged exposure to these fumes can result in respiratory illnesses. OSHA provides specific guidelines for welding operations, including the use of fume extractors and proper ventilation systems to minimize exposure.
Those pursuing an OSHA 30 Hour Certification will gain advanced knowledge in managing welding fumes and ensuring that proper safety measures are in place to protect workers.
5. Compliance with OSHA Regulations
5.1 Documenting and Reporting
Employers are required to keep detailed records of air quality assessments, ventilation system installations, and the training provided to employees. These records must be available for inspection by OSHA inspectors during routine checks.
An OSHA Certificate helps workers understand the documentation process and ensures compliance with all applicable regulations. Proper documentation can protect employers from legal and financial repercussions in case of workplace accidents.
5.2 Regular Inspections and Audits
OSHA mandates that employers perform regular safety inspections and audits of their workplace. These inspections focus on evaluating the effectiveness of air quality controls and PPE usage. By earning an OSHA Certificate, workers are trained to conduct these inspections and identify potential hazards before they become significant problems.
Conclusion
Reducing airborne hazards in the workplace is essential for protecting the health and safety of workers. OSHA guidelines provide a clear framework for employers to follow, including air quality monitoring, proper ventilation, PPE usage, and regular training. Earning an OSHA Certificate or OSHA 30 Hour Certification can significantly enhance workers’ and supervisors’ abilities to create safer working environments by implementing these guidelines effectively.
By following these safety measures and adhering to OSHAβs regulations, companies can ensure the long-term health of their employees while maintaining compliance with federal safety standards.
Leave a Reply