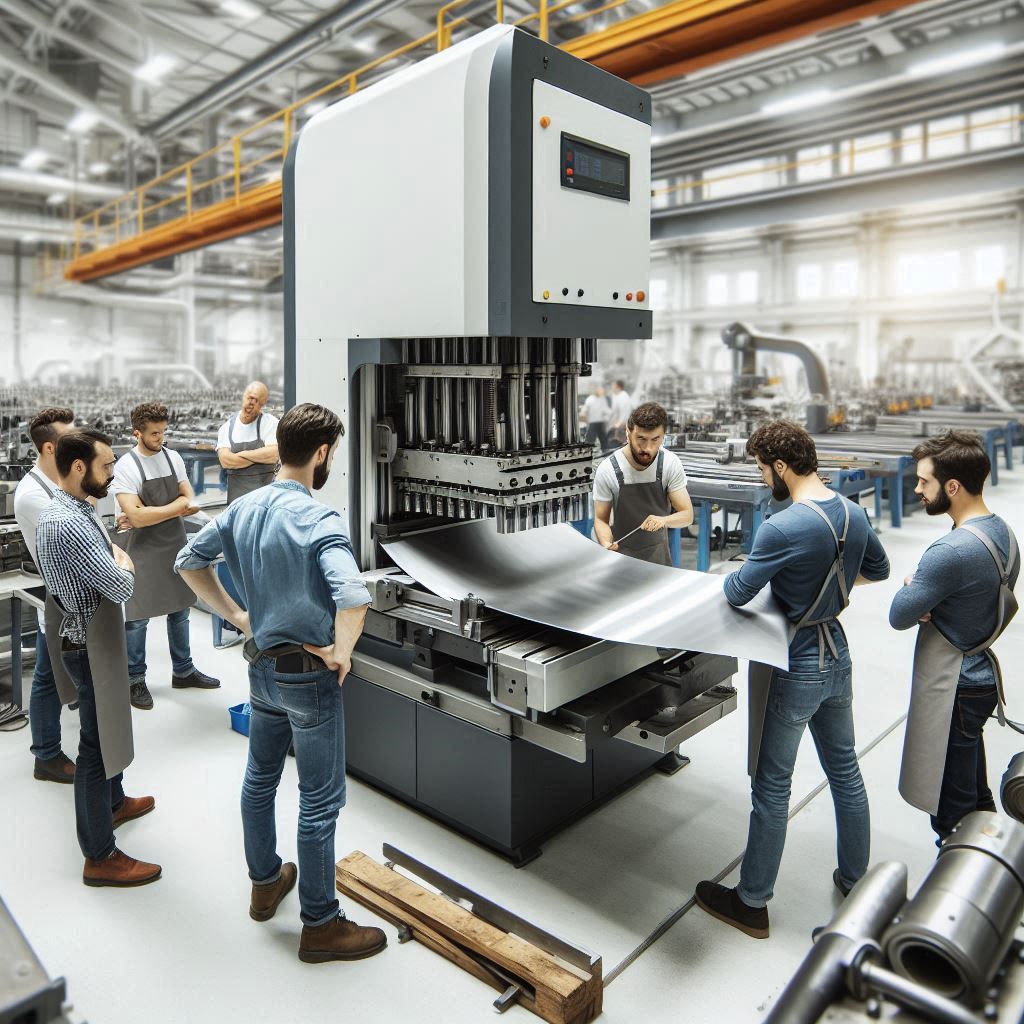
The fastest factories surely will change plate bending into a key process since, by that time, each fabrication process will have progressed to using these plates for such local trades as automotive, aerospace, building, and heavy equipment manufacture. For their powerful and precise bending movements, hydraulic plate bending machines have fit into the space as one of the most important tools in modern-day manufacturing. However, like any technology, these machines have changed through the years. Innovations in hydraulic plate bending machines have since incredibly improved their speed, accuracy, and overall quality of output. This article looks at how these innovations are rocking the industry and improving coming into play on the manufacturing floor.
Hydraulic Plate Bending Machines Defined
Hydraulic plate bending machines are those that bend plates, sheets, or coils into certain angles or curves by means of hydraulic forces. The machine typically consists of a lower bed, a top beam (ram), and a bending die that work together to form the material. The hydraulic system ensures that the machine can generate the force required to bend even thick and tough materials while offering smooth and controlled movements for precise shaping.
Bending systems employing hydraulic plate bending beams are preferred when bending must be done with the least operator involvement for maximum possible bending forces. Hydraulic plate bending machines may even be one of the most flexible machines and can also bend various other workpieces, like stainless steel, aluminum, and carbon steel, among others.
Innovations Scaling Measures to Improve the Speed and Quality of Operations.
1. Advanced CNC Control Systems
Advanced Computer Numerical Control (CNC) systems have introduced the greatest impact possible on the hydraulic plate bending machine. With the use of CNC control, the bending operation is automated by programming the machine to obtain specific bending angles and sequences.
Operators input parameters concerning configuration of the machine, such as material, security, bend angles, and any other information considered necessary. The ultimate result is that the machine automatically adjusts such parameters as speed, pressure, and stroke length. This increases the speed of production, and since human error is eliminated, quality and consistency are maintained; high-precision bends in complex configurations can be accomplished in less time by the manufacturer. The ability to store and repeat program further enables a faster turnaround for production setup being an added boost to productivity.
2. Faster Bending Speeds and Shorter Cycle Times
Historically, one of the challenges with hydraulic plate bending machines was the comparatively slow speed at which materials could be processed. Nevertheless, recent hydraulic technology innovations have developed rapid and efficient systems. Newer hydraulic pumps and valves allow faster force application with faster response time, making the machines able to finish bending cycles in lesser time.
Some of the newer systems, such as variable displacement pumps, optimize the energy consumption of hydraulic machines by adjusting the flow of the hydraulic fluid based on its real-time application. This means they provide the amount of power only as needed. This not only fastens the process but also economizes on the energy used, making it cheaper. Increased speed in bending and shorter cycle time in hydraulic machines result in increased production rates, which means manufacturers can now adhere to tighter schedule deadlines and increase volume production.
3. Multi-Axis Bending Capabilities
Another game-changing innovation is the multi-axis bending capability offered in hydraulic plate bending machines. Machines of historical standing would mostly lend themselves to single-axis bending, meaning that one had to reposition the material or the machine itself for every bent position and thereby sacrifice time and efficiency.
Modern Hydraulic Plate Bending Machine, however, allow bending across multiple axes simultaneously through multi-axis technology. This means that very complicated shapes can be fabricated with more speed and accuracy with less rework. The advantage of multi-axis capabilities extends to industries engaged in highly complex designs (like aerospace and the automotive sector) by diminishing number of operations to accomplish a project.
4. Automated Tooling Systems
Tooling is a major factor in plate bending, and traditionally, changing tools from one bending operation to another could consume considerable time in manual intervention. Automated tooling systems represent some of the latest innovations in hydraulic plate bending machines which allow for quick tool changes.
With robotic arms or automated tool changers, the operator can switch between various dies and tools in a seamless manner, allowing the machine to adjust according to the specific requirements of each part. This innovation reduces downtime between production runs and avoids human error involved in manual tool adjustments. This enhancement creates shorter and more efficient production cycles, and allows manufacturers to switch their focus to different projects without much interruption.
5. Enhanced Material Handling Systems
Material handling is one of the critical steps in the operations of plate bending. Innovations in hydraulic plate bending machine design now conjugate advanced material handling systems, like automated rollers, conveyors, and lifting systems, for the effortless movement of heavy plates into their position.
Hydraulic Plate Bending Machine manufacturers adopt green manufacturing practices in their manufacturing units. They build highly efficient machines that is capable of bending tough metal with ease using hrydraulic power. By complementing improved material-handling systems with advanced bending technology, overall speed increases, minimizing errors arising from improper material positioning.
Modern-day hydraulic plate bending machines are now installed with intelligent monitoring systems which give real-time feedback and diagnosis. Sensors installed in the machines monitor the machine continuously for pressure, temperature, line, and in-system performance.
This data further optimizes the bending process and correct condition calibration of the machine before it identifies any potential issues, which could lead to machine failure. Therefore, less unplanned downtime for manufacturers, steady production, as well as increased overall health for machines. At the same time, predictive maintenance technologies allow operators to even pre-emptively perform maintenance in order for it to work in a peak operating state without experiencing any once-in-a-while costly breakdowns.
Energy-Efficient Systems
These purchase energy but not always environment damaging energy consumption areas. These variables then have comprehensive environmental impacts considering how hydraulic plate bending machines generally used to consume lots of energy. Here come the challenges of innovation, of making even more energy-efficient hydraulic systems by optimizing hydraulic fluid flow and reducing energy losses and designing more modern machines for getting the needed power outputs while economically saving on energy.
Green hydraulic systems apply highly advanced materials and designs to lessen the wastage of hydraulic fluids, which means less pollution of the environment, very strict compliance with different regulations, and cuts in operating expenses. Energy-efficient systems are an attractive prospect to any company wishing to seek some improvement in sustainability in their manufacturing process.
Conclusion
To sum up, innovation drives a very fast change in production methods and techniques. Innovations in hydraulic plate bending machines have changed the way metal fabrication is done: Processes become faster, more accurate, and cost-effective.
Leave a Reply