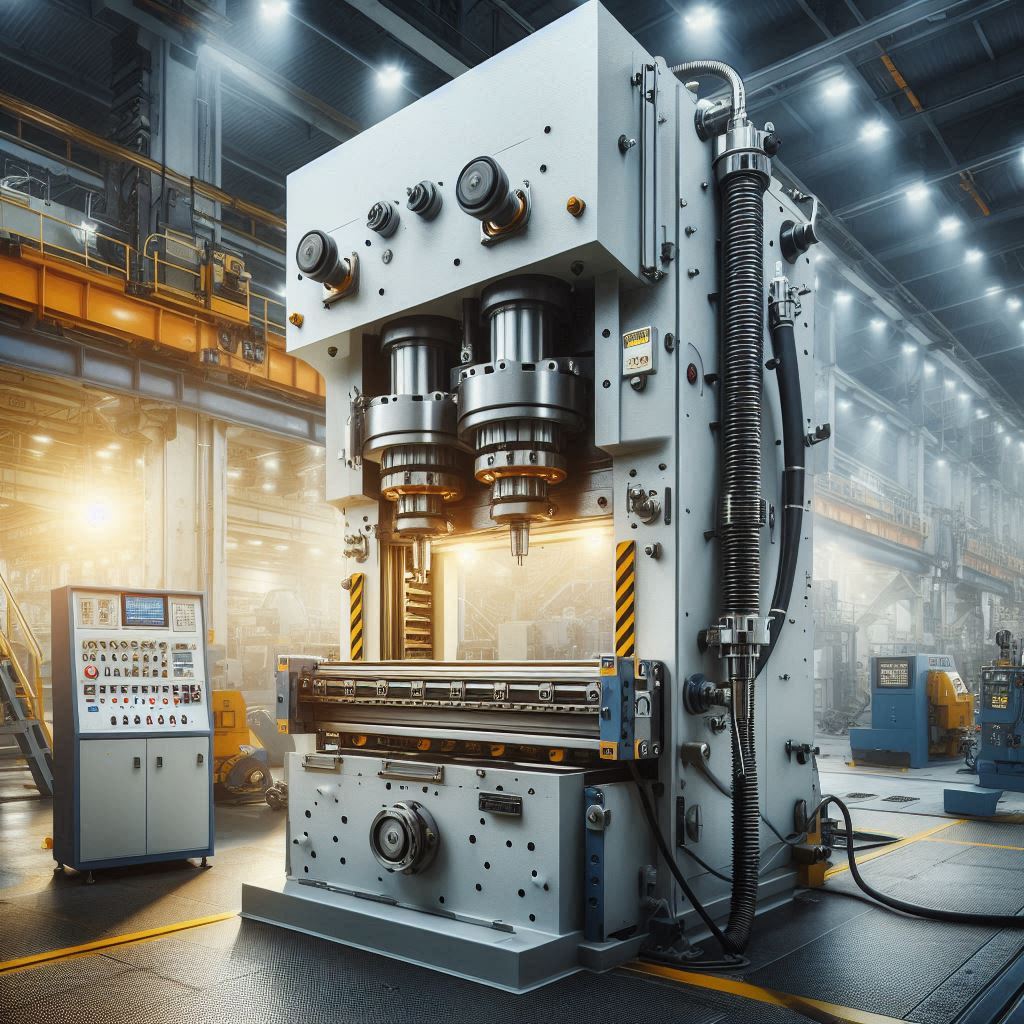
In the age of fast-paced world manufacturing, efficiency is the king. Industries across the world have not stopped searching for more ways of improving the production process, cost-cutting in the production, and making world-class products in minimum time. For Indian manufacturers, Hydraulic Press Brake Machines are one of these disabler tools from achieving the above goals.
Automotive, aerospace, construction, and heavy machinery are only a few examples of industrial and commercial sectors that are currently leveraging hydraulic press brake machines to revolutionize metal shaping and bending. With precision and versatility backed by power, hydraulic press brake machines are now the first choice for companies trying to keep progressing in this ever-difficult market. But what actually makes hydraulic press brake machines such a huge asset and how could they help skyrocket your manufacturing efficiency? Let’s explore that.
A hydraulic press brake machine definition is:
Hydraulic press brake machine is an advanced machinery for bending and shaping of metal sheets or plates with hydraulic force, applying pressure on the metal in order for it to bend at a required angle. These machines usually consist of a stationary bed, movable ram (top beam), and a die set that hold the workpiece while bending.
Dissimilarly from other bending tools, hydraulic press brake machines have unmatchable force, precision, and enable possible to bend different materials such as stainless steel, aluminum, and carbon steel. They are used generally in applications needing limited tolerances and complex bending finishes involving manufacturing of structural components, automotive parts, and large metal structures.
Unmatched Precision and Accuracy
One of the principal benefits offered by hydraulic press brake machines is accuracy. With the newest innovations such as CNC – computer numerical control technology, possible extremely precise bends can be achieved at tolerances as low as 0.01 mm in some cases. The angle of bend is fed into the controls by the operator, which then automatically adjusts all pressure, speed, and stroke length in order that the part achieves the required degree of bending.
This results in a tremendous amount of precision and minimizes possibilities of human error, the latter often being a major cause of defectiveness or rework because of manual machines. Given the repeatable consistent results, it allows producing a very high number of parts with uniform quality, which is very important for close specifications such as in Aerospace or Automotive Manufacturing.
Fasten production speed
While time is money in manufacturing, producing high-quality parts as quickly as possible is your best bet at enhancing productivity and profitability. Hydraulic press-brake machines are engineered for speed and thus require less time to produce high volumes of parts and objects.
The hydraulic system in these machines, as a matter of fact, delivers quick, constant force that guarantees shorter bending cycles compared with mechanical press brakes. Also with CNC controls, the manual adjustments or repetitive tasks are minimized as the portions can be programmed and automated bent sequences. All these features mean faster production and consequently lower downtime between jobs.
In addition, new hydraulic press-brake machines also incorporate automatic back gauges that adjust the workpiece’s position automatically, thereby reducing manual interventions to improve the production level further.
Versatility for Complex Bends and Shapes
The versatility of the hydraulic press brake machines makes them ideal for numerous applications. They can produce bends in varying sheet metal thicknesses and kind, from heavy-duty plates to thin gauges, with the same accuracy.
With all multi-axis bending capabilities and customizable tooling, these machines can create highly complex shapes and bends that may be impossible or very difficult to accomplish using traditional manual equipment. From a simple U-bend to a very complicated three-dimensional shape, hydraulic press brakes can do it all. This versatility provides manufacturers capability in a wider variety of jobs, possible areas to broaden their offerings to their customer base.
In the automotive industry or any other industry that depends on very complex parts such as body and frame of vehicles, hydraulic press breaks help manufacturers achieve intricate high-precision designs that fit seamlessly onto the assembly line.
Less Material Waste
Another advantage that hydraulic press brake machines present is the low waste of materials. Because these are precision instruments, the chance of defective or poorly bent parts being made is much reduced with bending angle made correct. Manufacturers can, therefore, get maximum use of their material, reducing scrap, maximizing the use of raw materials, by achieving the precise bending angles.
Most modern hydraulic press brake machines are also generally equipped with automatic nesting software, which solves the problem of material savings by finding the most optimal cutting patterns. In fact, it further reduces wastage of material, cost, and, ultimately, profit.
Increased Safety Features
Safety always becomes the number one priority in a manufacturing environment, while these hydraulic press brake machines have been developed bearing in mind quite a number of additional safety features that would protect both operators and machines. Laser safety guarding, pressure sensing, and an emergency stop button, which instantaneously halts the machine where errors are detected, fall under these safety measures.
Some hydraulic press brake machines have two-hand safety controls to keep the hands of the operator at a distance from the moving ram and tooling. Such safety systems installed in the machines ensure reduced accidents, fewer workplace injuries, and more safe conditions for the workers.
Energy efficiency costs savings
The developing hydraulic press brake machine saves that energy consumption cost for the manufacturers. The hydraulic system uses energy around when it is needed and then adjusts the speed and force to optimize it. Typically, these machines are equipped with energy saving modes along with eco-friendly hydraulic oils to reduce environmental impact. Continued energy and reduced material wastage due to hydraulic press brakes are long cost savings to companies, having valuable investments for manufacturers desiring higher profits with maintaining the production of high-quality output. Last but not least: The future of manufacturing efficiency. Today, the manufacturing companies could hardly be in action where they are in such stiff competition, aggressively pushing to improve efficiency and thereby reduce costs without sacrificing any quality.
Conclusion
The hydraulic press brake machine is probably one of the most powerful multifunctional machines that addresses both needs. Precision, production speed, less material wastage, and versatility in bending: these are the essential elements in how these hydraulic press brake machines are destined to transform manufacturers. Hydraulic press brake machine India make use of modern machinery in the manufacturing unit, plan, design, and engineer the hydraulic press brake machine that are efficient in forging tasks.
Leave a Reply