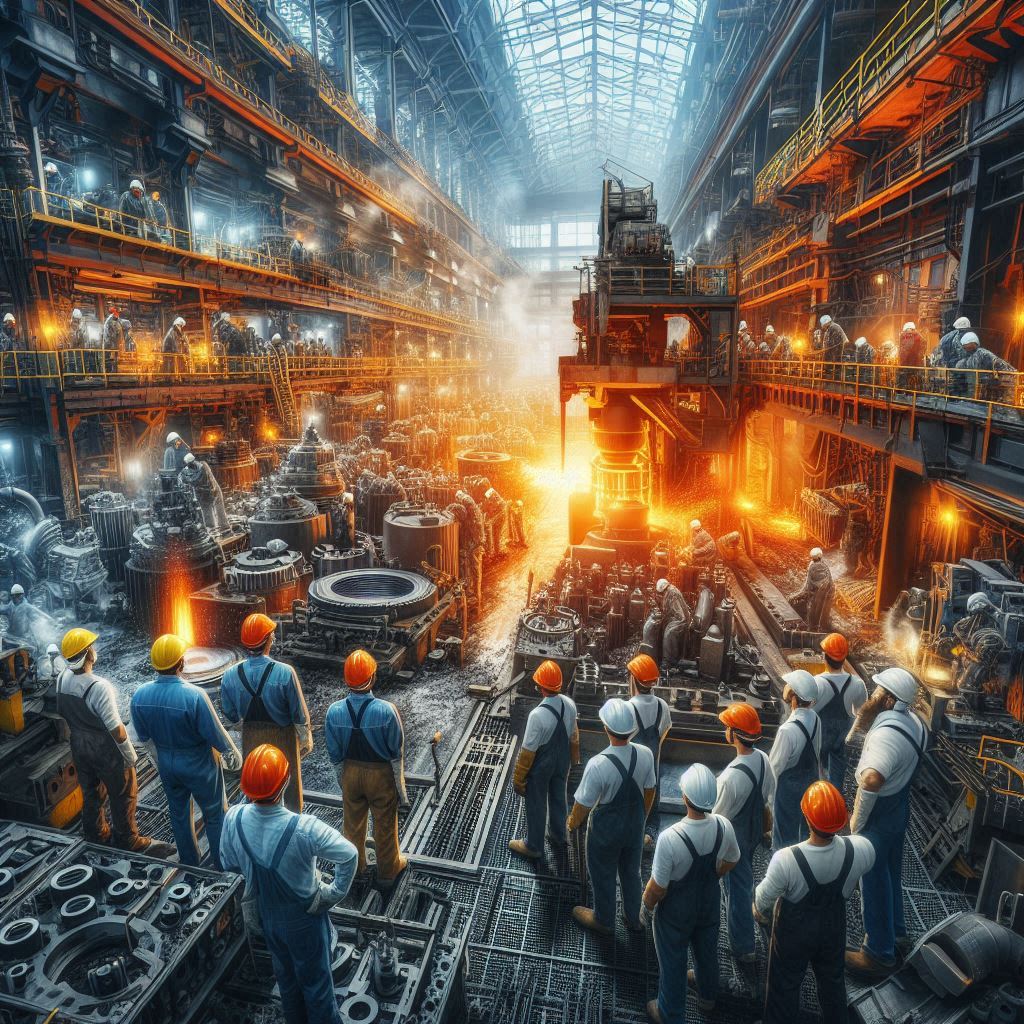
This is the most sophisticated and accurate manufacturing method to manufacture existing metal components of the highest surface finish quality, with extreme dimensional accuracy; it is popularly referred to as lost-wax casting. Foundries providing services in investment-casting manufacture parts for different fields or industries like aerospace, automotive, medical, and energy, among others. It is done in an advanced manner, coupled with strict quality controls and cutting-edge techniques-all to offer precision-engineered parts built under very stringent industry standards.
Understanding the Process of Investment Casting
Investment casting foundries involves several stages, starting with making the wax pattern, covering it with a ceramic shell, and melting the wax to leave a hollow internal mold. Some molten metal is poured into that mold, allowed to solidify, and then the shell is broken away to reveal the final cast components-hence, the term ‘investment casting’. It has several benefits such as excellent dimensional accuracy, geometry complexity, and low material wastage.
How Investment Casting Foundries Ensure Precision and Quality
1. High-Quality Raw Materials
Precision starts from raw material selection. Investment casting foundries work on well-focused investment in high-quality raw materials, including costlier alloys such as stainless steel, carbon steel, aluminum, or superalloys to ensure durability and performance. Rigorous inspection and testing of raw materials ensure the composition meets requirements in industry.
2. Advanced Wax Pattern Production
The wax pattern, which is a perfect image of the end product, determines a lot of accuracy. It allows investment foundries to manufacture highly durable and accurate wax patterns with high-precision injection molding machines. Most abnormalities and imperfections in the wax pattern get corrected at this stage before the process is transferred to thereafter.
3. Controlled Ceramic Shell Formation
To form an impeccable mold, the investment casting foundries apply multiple layers of ceramic slurry and fine sand into the wax pattern. The drying and curing phases are well managed so as to avoid cracks or deformities which would compromise the mold integrity under high temperatures during metal pouring.
4. Precision Metal Pouring and Solidification
Pouring of the metals into molds is most important for the quality in castings. Vacuum or gravity pouring methods are used in foundries to eliminate air bubbles, prevent oxidation, and promote uniform disbursement of metals. Controlled cooling and solidification enhance the structural soundness of the cast component.
5. CNC Machining and Finishing
The finished casting may be machined on a CNC machine as a final operation to attain tighter tolerances and finer details. Surface treatments such as polishing, heat treatment, and coating may be applied to give added corrosion resistance and wear resistance and improved aesthetics.
6. Stringent Quality Control and Testing
Strict quality control measures are instituted in every stage of investment casting production, including: Typical testing methods are:
- Dimensional checking-Coordinate measuring machines (CMM) measure and check whether it meets the standard goods’ requirements in tolerance level.
- Non-destructive testing (NDT): Internal defects are found by X-ray inspection, ultrasonic testing, and dye penetrant testing.
- Material Analysis β Integrity of materials is ensured by spectroscopy and hardness testing.
- Testing under Pressure and Load β Components are tested under real-life scenarios to evaluate their performance.
Conclusion
Investment casting foundries are committed to precision and quality through advanced manufacturing processes, rigorous testing, and continuous innovation. Their expertise in material selection, mold creation, metal pouring, and finishing work to supply industries with high-performance components that are reliable. These foundries can modify their techniques with advancements in technology to meet the ever-increasing demand for precision engineering characteristics among the different sectors.
Leave a Reply