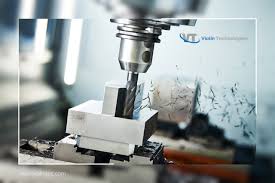
CNC (Computer Numerical Control) machining has revolutionized the manufacturing industry by enhancing speed, precision, and efficiency. This technology enables automated control of machining tools through computer programming, significantly reducing human error and increasing production output. CNC machining is widely used in industries such as aerospace, automotive, and medical equipment manufacturing, where precision and speed are critical.
The ability of CNC machining to produce complex parts with minimal human intervention has transformed traditional manufacturing methods. Unlike conventional manual machining, CNC machines follow pre-programmed instructions with incredible accuracy, ensuring consistent quality across production runs. This not only boosts productivity but also minimizes material waste and operational costs, making CNC machining an essential asset in modern manufacturing.
Enhancing Speed Through Automation and Efficiency
One of the primary advantages of CNC machining is its ability to significantly increase manufacturing speed. Traditional machining processes require manual adjustments, tool changes, and operator intervention, which slow down production. CNC machining automates these processes, allowing machines to operate continuously with minimal downtime. High-speed machining capabilities enable manufacturers to produce parts faster, meeting customer demands with shorter lead times.
Moreover, CNC machines can perform multiple operations in a single setup, reducing the need for repositioning and recalibrating workpieces. This streamlines workflow, optimizes cycle times, and ensures rapid production of high-quality components. With advancements in software integration and real-time monitoring, manufacturers can further enhance production speeds while maintaining precision and efficiency.
Precision and Accuracy in Component Manufacturing
CNC machining is renowned for its exceptional precision, ensuring components meet strict tolerances and specifications. The computerized control system eliminates the inconsistencies associated with manual machining, delivering parts with high repeatability and uniformity. Whether producing intricate aerospace components or medical implants, CNC machining guarantees exact measurements and flawless finishes.
Additionally, modern CNC machines feature advanced sensors and feedback systems that continuously monitor and adjust machining parameters. This real-time correction mechanism ensures parts remain within designated tolerances, reducing errors and minimizing rework. The ability to maintain high levels of accuracy enhances product quality, improves reliability, and strengthens a manufacturer’s competitive edge in the market.
Cost Savings and Waste Reduction in Manufacturing
Efficiency in material usage is another significant benefit of CNC machining, leading to cost savings and waste reduction. Traditional machining methods often result in excessive material waste due to manual cutting errors and inefficient tooling. CNC machining optimizes material utilization by following precise cutting paths, reducing scrap, and maximizing yield from raw materials.
Furthermore, the automation of CNC machining reduces labor costs by minimizing the need for skilled operators. Once a CNC program is set up, machines can run autonomously with minimal supervision, allowing manufacturers to allocate human resources more effectively. This cost-effective approach enhances overall profitability while maintaining superior production standards.
Future Trends and Innovations in CNC Machining
The future of CNC machining is driven by advancements in artificial intelligence (AI), automation, and additive manufacturing. AI-powered CNC machines can analyze data in real-time, predict tool wear, and optimize machining parameters for enhanced performance. These smart machines improve efficiency, reduce maintenance costs, and minimize production downtime.
Another emerging trend is the integration of CNC machining with 3D printing technologies, enabling hybrid manufacturing solutions. This combination allows manufacturers to create complex geometries, prototype faster, and customize products with greater flexibility. As CNC machining continues to evolve, its role in high-speed, precision-driven manufacturing will remain indispensable, shaping the future of industrial production.
Conclusion
CNC machining has become a cornerstone of modern manufacturing, significantly improving speed, accuracy, and efficiency. By automating processes, reducing errors, and optimizing material usage, CNC machines enhance productivity and cost-effectiveness. As technological innovations continue to advance, CNC machining will play an even more critical role in driving manufacturing excellence, ensuring businesses stay competitive in a rapidly evolving industry.
Leave a Reply