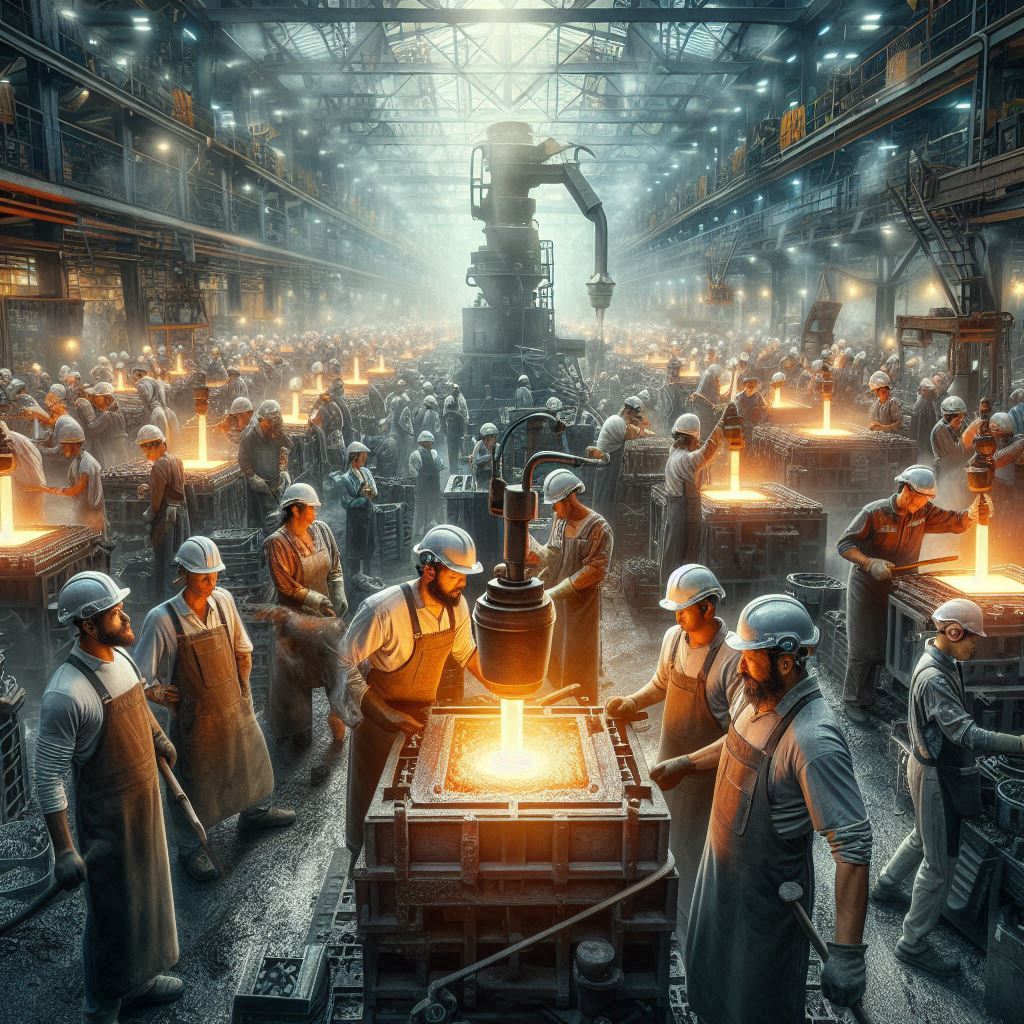
Being notable manufacturers recognized for the production of quality cast components for industries ranging from automobiles to aerospace, defense, and heavy machinery, Indian casting companies act as the backbone of global manufacturing. The rising demand for precision-engineered products has put quality and accuracy in casting processes as a priority. With strict adoption of quality control, modern technologies, and industry best practices, precision and consistency are maintained by manufacturers in the Indian casting industry.
Prominent Quality Control Steps Used by Indian Casting Houses
1. Raw Material Inspection
The crux of precision casting remains with using the best-quality raw materials such as iron, steel, aluminum, etc., and specialized alloys. Indian foundries perform:
- Chemical Composition Analysis – Specified by international standards using spectroscopic technology.
- Purity and Strength Testing – Assures integrity of metal to prevent impurities that could affect the quality of the casting.
2. Advanced Casting Procedures
Depending on the application and required precision, various methods of casting are employed by Indian casting companies:
- Investment Casting – Usually considered for aerospace, automobile, or medical components usually requiring high accuracy and fine surface finishing.
- Sand Casting – Suitable for large complicated parts typically involved in heavy machinery and industrial applications.
- Die Casting – Mass production for intricately designed, thin-wall components for the automotive and electronics industries.
3. Precision Mold and Pattern Making
This scene states that the quality of molds or patterns corresponds directly with the quality of the end cast product. A variety of modern developments are being applied by Indian casting manufacturers that include:
- CNC Machining for Pattern Making – Provides a good representative pattern for high dimensional accuracy.
- 3D Printing Technology – Rapid prototyping of molds helps enhance precision and development time.
4. Rigorous Process Control and Regulation
To set the environment conducive for precision during the casting process, Indian foundries utilize:
- Automated Pouring Systems – Attempting to remove as many human errors as possible and maintain uniformity.
- Control Over Temperature and Solidification – A way to prevent defects like shrinkage, porosity, or cracking.
- IoT systems – For real-time monitoring of parameters such as metal flow, cooling rate, and mold integrity.
To Know How to Inspect & Test for Quality Assurance
5. Non-destructive Testing
These types of techniques help in identifying both internal and external defects without subjecting the material to any distress. Some of the most widely used techniques include:
- X-ray Radiography – is used to detect internal defects such as porosity and cracks.
- Ultrasonic Testing – is used to evaluate the integrity of a material and to find hidden discontinuities.
- Dye Penetrant and Magnetic Particle Testing – For surface defects interrogation and assurance of structural integrity.
6. Dimensional and Surface Finish Inspection
To meet high accuracy demand, Indian foundries use:
- Coordinate Measuring Machines (CMMs) β For accuracy in dimensions, to a level of micrometers.
- Surface Roughness Testing β Measurement of smoothness preventing defects from machining. Inspection of the following types:
Mechanical and Chemical Property Testing
There are various tests performed on strength and durability of cast components such as:
- Tensile and Hardness Tests β Detect the strength of the material as well as resistance in deformation.
- Corrosion and Heat Resistance Tests β Used in ascertaining durability in extreme environments.
Continuous Improvement and Industry Compliance
8. Following the Global Standards
Indian casting industries pride themselves in following international quality standards such as:
- ISO 9001 & IATF 16949 β Automotive Quality Management System.
- AS9100 β Aerospace industry compliance.
- Needed NADCAP Certification β for use in critical aerospace and defence applications.
Adopting Lean Manufacturing and Six Sigma Methods
Most foundries use Lean and Six Sigma principles for avoiding waste, improving process proficiency, and enhancing quality in an overall setting.
Conclusion
With these manufacturing techniques from the advanced level, a rigorous quality control process, and continuous improvement strategies, Casting company India will ensure quality and precision. Combining modern technology with global and basing on innovation, such companies are definitely securing a place for themselves among the frontrunners in the casting global industry. The demand for high-performance components keeps increasing, and Indian cast component manufacturers remain committed to providing excellence in every cast product.
Leave a Reply