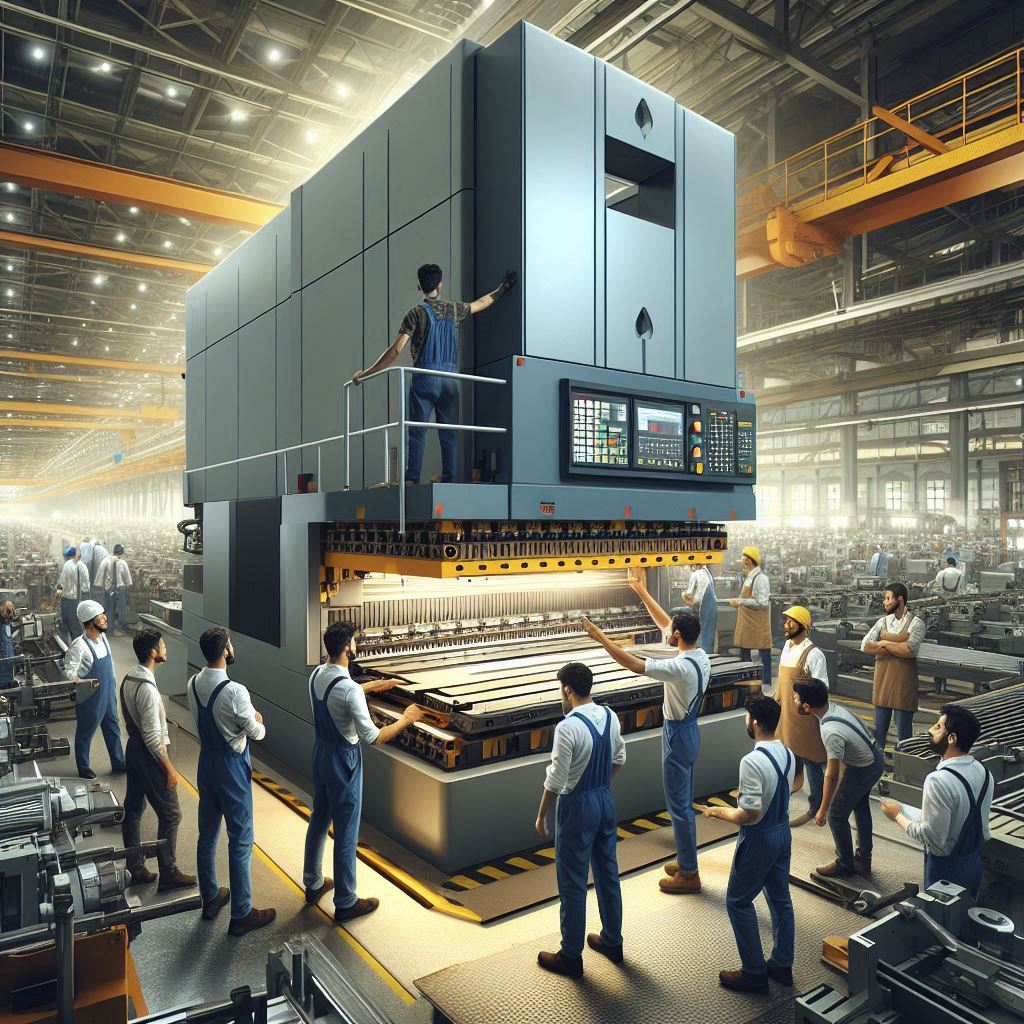
NC (Numerically Controlled) Press Brakes are vital in bending metal accurately and efficiently. However, poor usage could lead to inaccurate bending, rejection of materials, and, in the worst cases, damage to the machine. Maximizing productivity and maintaining quality output can be achieved by avoiding these common mistakes:
1. Incorrect Tooling Selection
Some punch-and-die combinations are unfit for application, which severely impairs the quality of the bends, resulting in defects such as too much bending, the cracking of the workpiece, or distortion. There must also be different setups of tooling for different metals and thicknesses to achieve accuracy and repeatability. A die opening that is less than what is called for in the design could cause the material to be stressed more than necessary and damage the part along with the die, affecting efficiency. Choose die openings according to material thickness for even distribution of forces, and select punch angles that correspond with the required bend angle to avoid overcompensating or weakening the bends. Besides that, the proper maintenance of tooling through periodic inspection and replacement of any worn-out component enhances precision, prolongs tool life, and prevents costly errors in production.
2. Improper Material Positioning
Misalignment of the workpiece during bending may cause uneven bends that translate into bad parts with an increase in material waste and rework. Many factors account for positioning errors, such as inaccurate settings on the back gauge or mishandling by the operator. These errors create inconsistencies in the final product. Even slight misalignment can translate into a series of cumulative errors that build up, especially in finish-oriented industries. To stave off such issues, operators should always verify the settings of the back gauge before every operation to ensure proper positioning. The use of reference marks or laser alignment systems can greatly improve accuracy by providing visible aids to alignment. Additionally, ensuring that operators are trained in correct material-feeding and positioning techniques will help foster consistency, accelerate production, and minimize errors.
3. Ignoring Machine Calibration
An under-calibrated NC Press Brake can lead to inaccurate bends, material waste, and inconsistent production quality over time. Even the smallest amount of calibration error will produce a deviation of angle and alignment, which will cause defects that could lead to rework or scrapping. These inaccuracies lead, in turn, to increased cost and decreased efficiency in workflow. Maintenance of precision implies regular machine calibrations per the manufacturerβs guidelines. It is critical also to treat mechanical wear of key components, such as the ram, back gauge, and tooling because such an investigation would serve to uncover emerging problems before they affect performance. Whenever there is a change in material or thickness, the settings on the machine must be adjusted to ensure that every bend fulfills the required specification, thus enhancing uniformity across the board while minimizing production errors.
4. Overloading the Machine
Excess overloading of an NC Press Brake poses unaesthetic consequences that adversely affect the machine’s performance, included among them being failure of working stages, breakage of tools, and mighty injurious prospects for operators. An excessive load on the machine induces high strain in its hydraulic system, frame, and tooling, yet another layer considered for early wearing out, misalignment, or even catastrophic failure. Furthermore, adding excess sideways pressure would also bring on cracking or warping of tools, which would mean bending will no longer be done with the required accuracy, thus causing rise in cost. To avert this calamity, operators should deter from overloading the NC Press Brake and rather consult the tonnage capacity of the machine before any bending activities can begin. Equally distribute the load onto the tools for maintaining tools’ stability and overcome undue strain on one spot. Calculate the tonnage carefully, keeping safety in mind, thereby ensuring protection for equipment and the operator while achieving accuracy in the bending process.
5. Neglecting Safety Measures
Failure to follow safety measures while operating an NC Press Brake india can lead to deathly injuries from crushed hands, or the risk of metal snapping back. Many operators speed up production by crowding moving parts, increasing the chance of an accident. Far from merely applying to worker safety, negligence of these practices also retards production and exposes the company to litigation. Operators should wear protective gear such as gloves and goggles at all times to create a safe working environment. Emergency stops and safety guards and machine barriers can all be used to prevent accidents. Safe working procedure training must be comprehensively developed, ensuring all operators understand the hazards associated with the operation of this equipment and best practices to limit such risks.
6. Skipping Regular Maintenance
Routine upkeep on an NC Press Brake, if neglected, creates severe operational issues: hydraulic leaks, variable bending accuracy, and premature wearing of the primary parts. Rather, skipping lubrication would lead to wear between all the movable parts due to friction, eventually causing machine breakdown and expensive stand-downs. This also allows hydraulic systems, if not kept in check, to leak or have insufficient fluid level, throwing the machine’s pressure control and performance out of whack. All these troubles could be avoided with a maintenance timetable-in fact, lubrication performed on the machine following the manufacturer’s recommendations, inspection of hydraulic systems for leaks and optimal fluid levels. Ensuring a clean machine environment, free from dust and debris, would also contribute to its efficiency during operation, hence aiding in prolonging life and smooth precision operations.
7. Wrong Bending Sequence
Bending parts out of order poses problems for handling and assembly and interferes with achieving accuracy for the final product. Interference problems for the operator become harder; bends become taxed and hard to complete, components may not fit rightly. All of this adds to wasted material, reworked parts, and delayed time in production. This highlights the need for properly planning the bending sequence in advance, which allows each operation to facilitate the following one trending. Testing one prototype piece makes it possible to foresee potential issues way early, saving a lot of time and resources. Moreover, simulation software for bending gives an insight into the work process and enables operators to visualize and deal with potential sequencing problems even before the real job is out.
Conclusion
Avoiding such commonplace errors will improve productivity, reduce scrap, and extend the life of the NC press brake. Training, keeping up with maintenance, and an eye on the details will get you high, consistent quality bends.
Leave a Reply