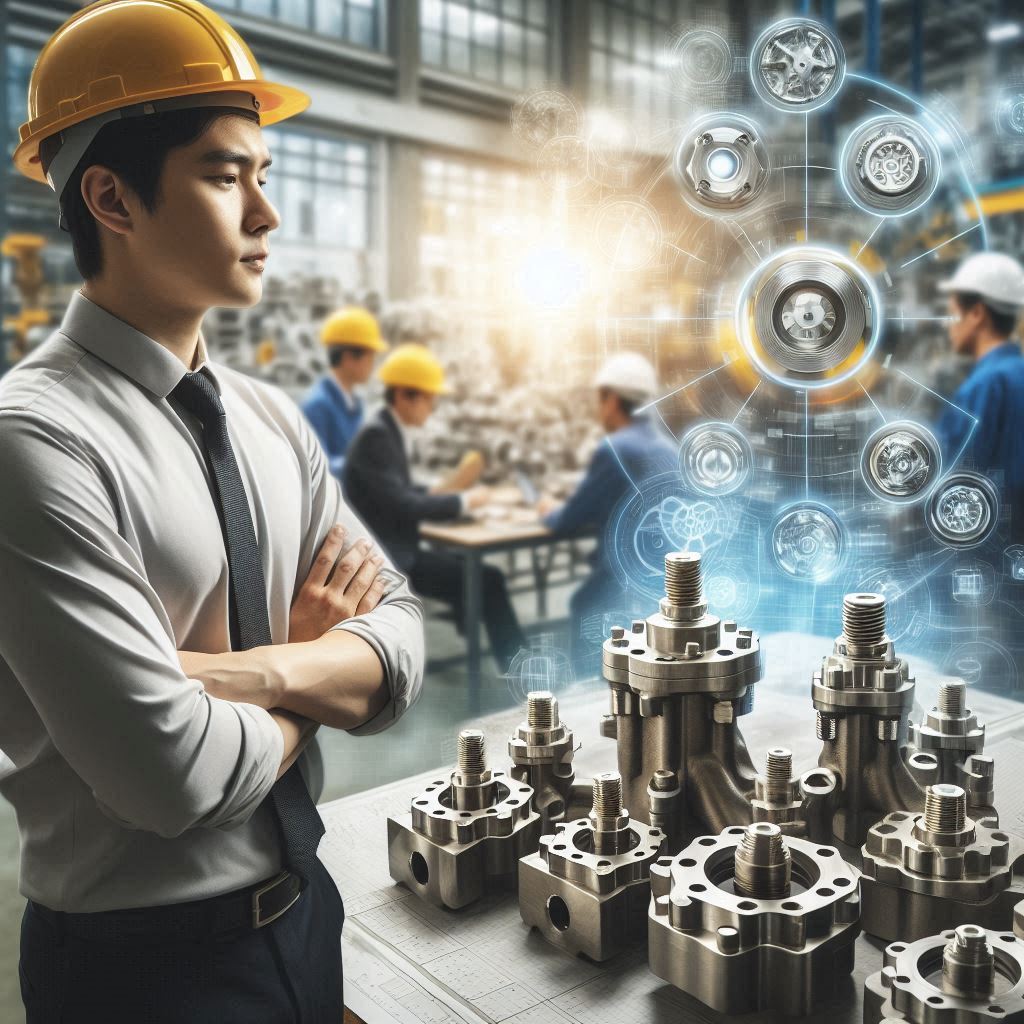
A valve casting supplier that is suitable gets serious attention. Valve castings form an important aspect in oil and gas, water treatment, power generation, and chemical-industrial processes. These vital pieces of machinery control the flow of fluids and gases in the concerned systems; therefore, quality and reliability of valve components are of utmost importance. Hence, whether it is for new-designed valves of the new plant or component replacement for existing infrastructure, the choice of a reputable valve casting supplier is paramount to ensure the future success of the whole project. This article discusses some of the crucial factors to take into account when choosing the most suitable valve casting supplier according to one’s specific needs.
1. Experience & Expertise
When it comes to the selection of Valve casting supplier experience and competence related to the relevant field are among the prime considerations. A supplier possessed of long-standing experience in the industry would be able to produce high-quality valve castings, which would have to be in conformity with stringent requirements as to performance and safety. Moreover, since, at times, several of these challenges would differ from one industry to another, any credible supplier will recognize the specific challenges concerning casting of valves, be this relating to controlling extreme temperatures and pressures, for corrosive or abrasive fluids, or for both. Check for a supplier with know-how on the casting of the specific type of valve you need-whether ball valve, gate valve, globe valve, or check valve.
2. Material Capabilities
Valve bodies are made with different kinds of materials such as stainless steel, bronze, cast iron, and alloys like Inconel and Hastelloy. The choice of material is based on factors such as the environment in which the valve is going to be used, the type of fluid being controlled, and relevant pressure and temperature specifications; a good valve casting supplier should be capable of handling various materials and alloys, therefore fitting the requirements for your particular application. They should also have efficacious expertise in selecting materials that guarantee durability and corrosion resistance in conjunction with the working conditions of the system.
3. Casting Process and Technology
How the supplier casts its products will predominantly determine the quality of valve castings. Sand casting, investment casting, and die casting are the general types of techniques for valve casting employed. Each method has its advantages dependent on the different sizes and complexity of the valve. Investment casting, for example, is superb for producing small, precision valves that are highly intricate and detailed. Sand casting is, however, the technique which works best for larger, complex valves. The supplier should also be well equipped with advanced technology such as CAD/CAM for precision design and prototyping. This ensures that your casting is done right and the technical specifications are therefore all met in order to minimize any defects and rework. Finally, the suppliers must stay current with trends in casting materials and techniques to guarantee quality products at minimum cost to clients.
4. Negotiable Weight and Advantages
Valuable time and great costs are two significant criteria for choosing a valve casting supplier. A good supplier should ensure timely delivery of your periodical orders at a reasonable cost and without compromising on quality. Lead times will ideally be open for negotiation right from the start, as casting delays may hinder the progress of your project. The total cost associated with purchasing castings should necessarily include not only the apparitions of value but also for expenditures related to machining, finishing, and quality inspection.
5. After-Sales Support and Communication
Lastly, customer support and proper communication matter when selecting a valve casting supplier. The supplier should be proactive and willing to work with you on the design, production, and testing stages. An engaging supplier, providing technical support, and proactively working with you solve any issues or concerns assures that the valve castings will truly be to your satisfaction.
Conclusion
Selecting a valve casting supplier involves examination with regard to its experience, material capabilities, casting processes, quality assurance procedures, lead times, and customer support. And after weighing all these parameters, you can reasonably say that you can partner with and win a worthy supplier that will deliver the assurance of a dependable valve casting that meets your specification, while also ensuring the growth of your system in due course. A dependable valve casting supplier guarantees your precision, durability, and performance requirements for influencing the efficiency of your operations.
Leave a Reply