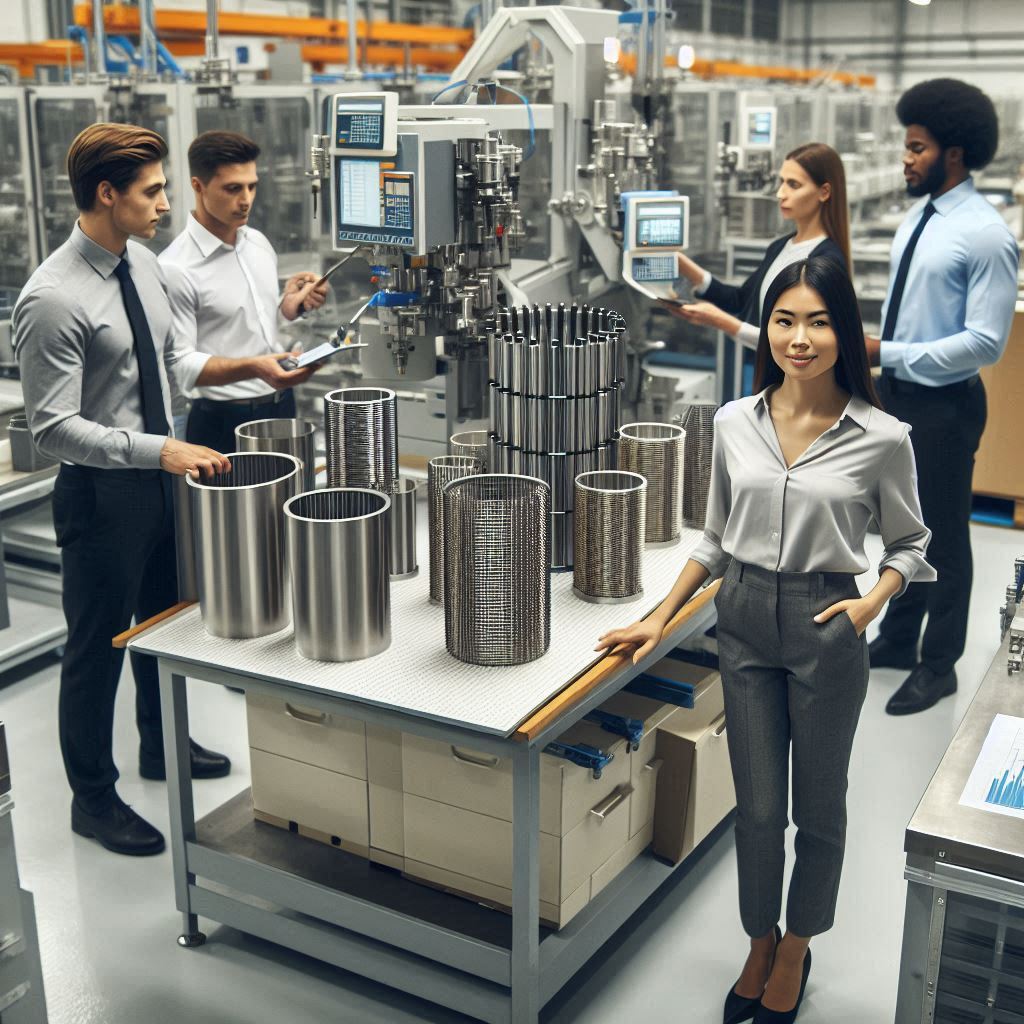
Y-Type strainers are vital components within the industrial pipeline system to separate the liquid and gas streams from debris, dirt, and solid materials. Further, they also prevent damage to pumps, valves, and sensitive longitudinal equipment with regard to performance longevity. The manufacturing process adopted for Y – Type strainers gives a deep understanding of the quality, durability, and performance of the strainers in different industrial applications.
Choosing Raw Materials
The whole process of manufacturing starts from the choice of good quality raw materials. The raw materials selected for this process are – stainless steel, carbon steel, cast iron, and bronze. All these materials are selected depending on the application. The material should be resistant to corrosion, pressure, and very high temperatures to ensure longer efficiency and life of the Y-type strainer.
Design and Engineering
The construction of the Y-Type strainer initially starts with machine coding in terms of advanced CAD software by manufacturers. The precision design that will cater for the requirements of ASME, ANSI, or DIN specification turns into manufacture. While undergoing these stages of design as the strainer construction sequences associated with the flow rate and actual filtration will meet structural integrity considerations.
Garment and Castings
The design is finalized and then fabrication starts. The Y-Type strainer body is made using casting, wherein hot molten metal is poured into molds to acquire the desired shape. To achieve the dimension and smooth finish, CNC is employed for precision in Computer Numerical Control machining.
Perforated Screens and Mesh Assembly
One component of the Y-Type strainer is the straining element, which consists of a perforated metal screen or wire mesh. These are manufactured separately and later grouped into the strainer body. Their screen size and mesh type differ based on the application filtration requirement.
Welding and Surface Finishing
Sometimes, the need is for welding to ensure tight fastening. The welds are checked against the industry specifications for strength and durability. All surface finishes galvanization, epoxy coating, or polishing are applied for the resistance to corrosion and higher life.
Quality Assurance and Testing
Such thorough quality tests are administered on Y-type strainers before testing their endurance capabilities:
- Pressure Testing: The strainer is subjected to high-pressure conditions to identify areas of susceptibility to leak formation.
- Flow Testing: It verifies that the strainer allows the desired fluid flow while thoroughly filtering out debris.
- Dimensional Accuracy Check: This checks whether the strainer conforms to design specifications as well as any tolerances.
- Material Inspection: This ensures the composition and quality of raw materials with respect to manufacturing.
Final Assembly and Packaging
After passing all of the above quality tests, the Y-Type strainer is assembled with all relevant parts, such as flanges, bolts, and gaskets. Secure packaging protects it from damage during transport and storage. Indicate the specification, pressure ratings, and material composition with proper labeling.
Conclusion
The Y type strainer manufacturerΒ adopts a blend of precision engineering with high-quality materials and rigid quality control measures. Using a much-detailed process allows manufacturers to create strainers that can meet industrial demands on efficient filtration while concurrently providing longer service in pipeline systems involving various industries, including those that treat water, oil and gas, as well as chemical processing.
Leave a Reply