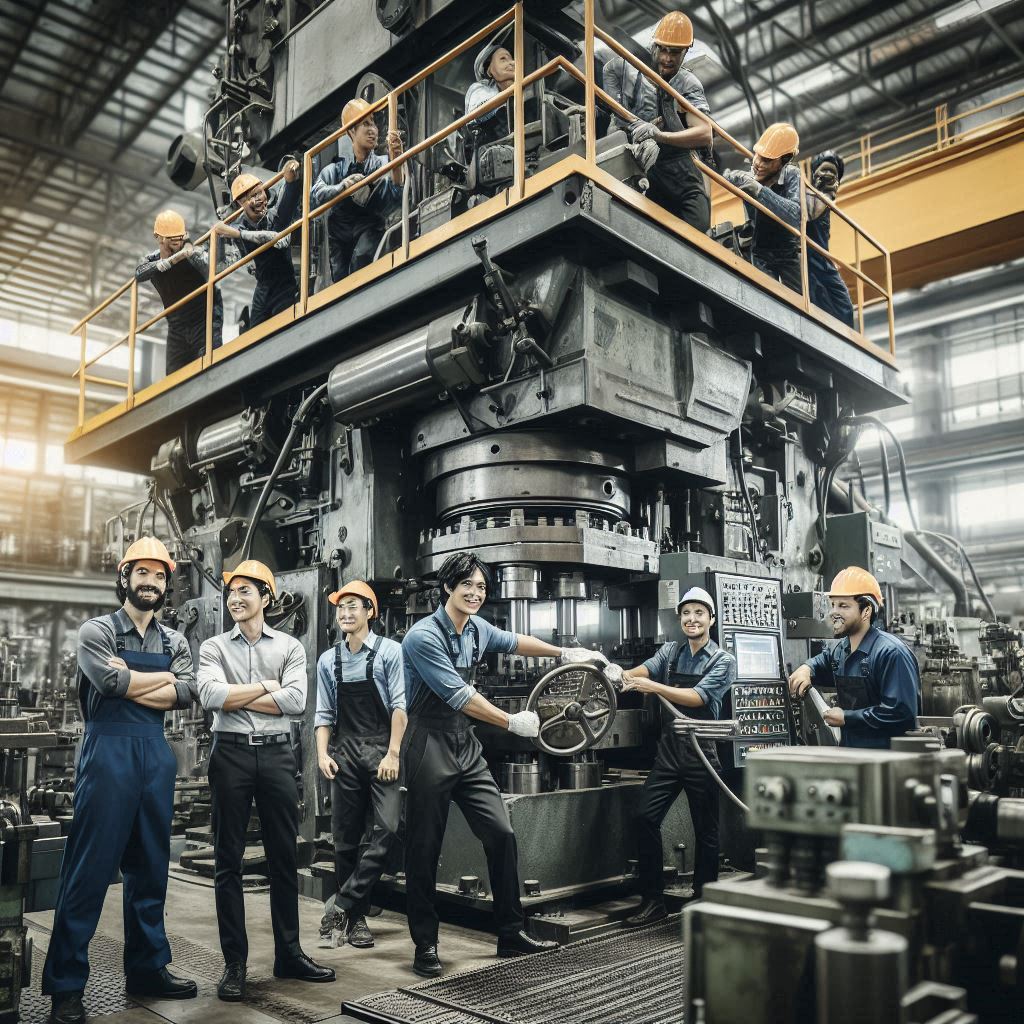
Metal bending proves to be an indispensable process in various manufacturing industries and uses several fields, which include automotive, aerospace, construction, and even metal fabrication. Manual bending is a methods of performing the bending using simple hand tools like hammers, clamps, and vises. The most recent advances in technology have made the bending process very efficient, fast, and precise with the introduction of Press Brake Machines. But is the change really worth it? The honest-to-goodness truth is that the difference is huge; hence, companies that didn’t adapt would find themselves lagging in the race against their competitors.
Enter the full-blown comparison of Press Brake Machines vs. Conventional Bending and let the details set one straight on why modern Press brake machine manufacturer have made the switch!
1. Precision and Accuracy β The Game Changer!
Traditional bending depends on manual effort and skill of the operator and is a source of error and inconsistency, especially in case of complex shapes. Here, CNC controlled press brake machines deliver pinpoint accuracy, uniformity of bends, and minimal waste of material ensuring precision for each and every job. For those who need top-notch accuracy from their jobs, traditional processes just can’t compete with modern presses.
2. Speed and Efficiency β Time is Money!
Compared to current production speeds, conventional bending is typically performed by hand, so very slow and labor intensive-almost every shape might need readjustment or even completely changing to create this part shape. One of the most important operations for press brakes is its speed in production. The bending action through press brake machines can be automated and done within a short period for several sheets at a time. This translates to lower manpower requirements and increases productivity while reducing manufacturing time, making press brake machines a must for high-demand industries.
3. Strength and Capability β Heavy Weight Handling
Heavy-duty applications cannot use manual bending because, due to the limitation of manual force, it cannot bend thick or hard metals. Manual bending is also very tiring and requires a lot of physical effort. On the contrary, heavy duty equipment for bending tough materials like thick steel, aluminum, or any material of difficult nature, is press brakes that work with hydraulic or mechanical force. These machines are really ideal for industrial projects on a grand scale as they ensure performance, power, and above all, accuracy-another reason to choose press brake machines above all.
4. Safety β Guarding Workers from Injuries
Because of manual handling, traditional bending is more accident prone than modern techniques and usually results in hand injuries, strains, and injuries from metal recoil with no safety features built into the process. Compared with press brake machines that are fitted with safety interlocks, sensors, and emergency stop systems, this greatly reduces the risk of direct human contact with heavy material decors from sharp edges. The press brake machine reduces workplace injury, thus making the place safer, more productive, and more efficient.
Β
5. Cost and Investment-Which is More Economical?
Conventional bending is initially less expensive but incurs huge future costs due to increased labor cost and material wastage due to human error. The opposite is true with press brake machines. Their high initial investment for equipment becomes a quick payback by automating the process, resulting in reduced labor dependency and reduced material wastage. So at some point, press brake machines turned out to be the quite economic and efficient solution for metal fabrication businesses.
Final Verdict-Which Is Better?
If the metal bending applications are limited and few, being rather smaller, then traditional methods can still be useful. But, when we are to factor precision, speed, safety, and cost-effectiveness into the equation, nothing but a Press Brake Machine will prove to be the best option! Manual bending is quite the outdated practice now, and businesses investing in press brake technology are reaping a massive competitive edge. Don’t get left behindβupgrade to something new and ahead in the industry!
Leave a Reply