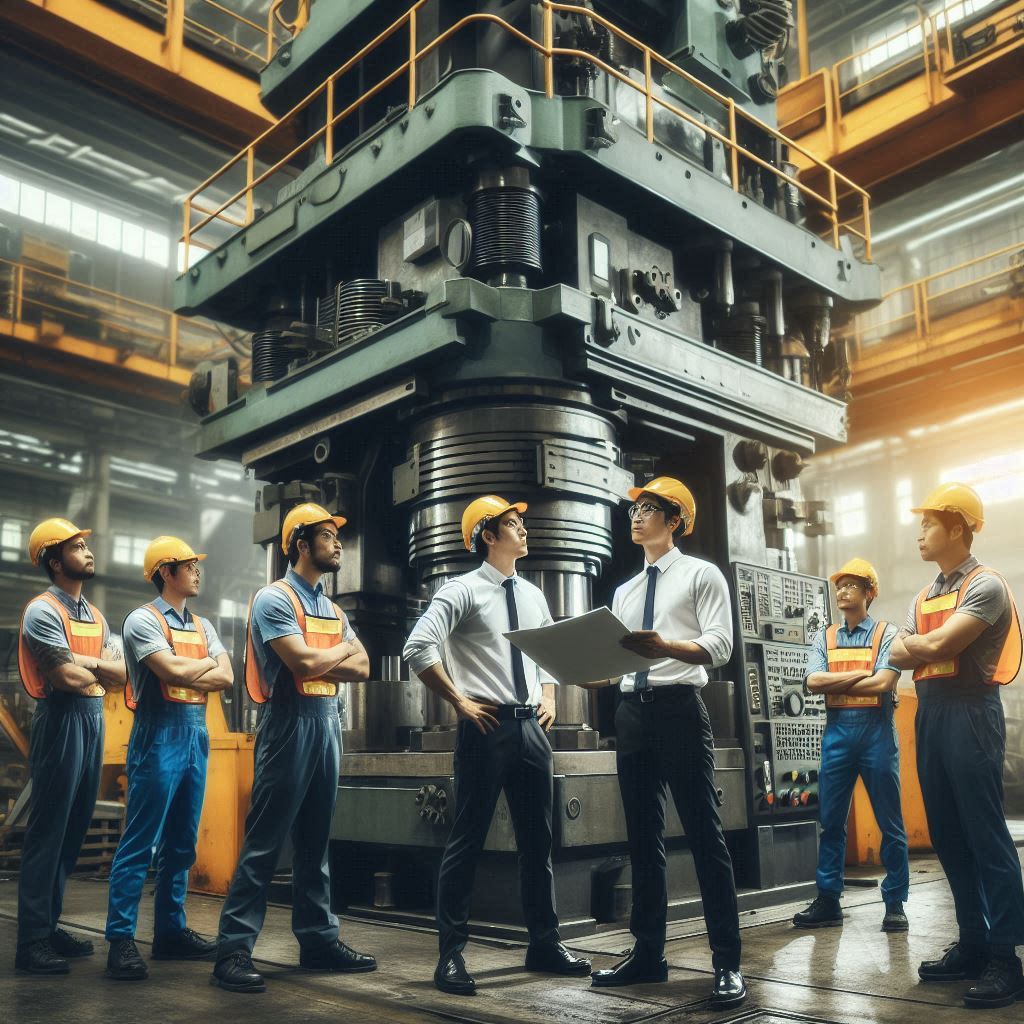
For long time users of metal fabrication, power press machines permit manufacturers to very efficiently cut, punch, bend and shape metals. As the industries evolve, so does the story of power press machines with increasing developments in the areas of precision, automation, and sustainability. Thus, automation, IoT integration, energy-efficient and safety features are poised to determine the fate of power press machines. This paper will dwell more in the major trends and innovations in metal fabrication defining the future of power press machines.
1. Automation and CNC integration
The revolution of power press machines, probably the greatest, has always been towards automation with increasing amount of Computer Numerical Control or CNC involvement. Earlier power press machines used to operate only with manual labour and very skilled operators were involved during stamping and pressing in factories. Today, modern machines have been equipped with a CNC control system and are thus capable of operating precisely without an element of human mistake while they enhance overall productivity because of automation.
Automation makes it possible for the Power press machine manufacturer to perform even very complex operations with very little supervision, hence accelerating production immensely. With further adoption of robotic arms and automated material handling systems into manufacturing, this development will continue to proceed further.
2. Smart Manufacturing and IoT Connectivity
Industry 4.0 and IoT connectivity will usher in a new realm of modern possibilities that power press machines would ever realize. Those will include predictive failure and production efficiencies and even remote monitoring and control to minimize downtime and improve output performance in Iot-enabled machines. Therefore, as more manufacturers move toward smart factories, IoT-integration features shall soon become the new standards among modern power press machines, together with predictive maintenance.
3. Energy Efficiency and Sustainability
Energy efficiency and sustainability are among the hottest topics in modernity, and today’s power press machine is designed to consume less energy and have a lower footprint in terms of environmental impact. Hydraulic and servo-electric models are being more preferred because they need less energy. Advancements such as regenerative braking systems, non-toxic lubricants, and state-of-the-art cooling mechanisms promote less waste and less operating expense. Thus, these innovations further the global sustainability ideals to make the power press machine environmentally friendly and cost-efficient.
4. Enhanced Safety Features
Above all, metal fabrication should ensure safety at the worksite, and the future power press machines will be equipped with advanced safety features such as light curtain sensors, two-hand control systems, and AI safety mechanisms. These technologies will help the operator be protected from hazards by identifying unsafe conditions and preventing inadvertent activation. Such technologies will be able not only to detect unsafe conditions but also to prevent accidental activation and anticipate possible malfunctions, thus contributing to the reduction of work-related injuries as well as increased safety within the workplace.
5. Customization and Flexibility
More customization in the future will be provided for power press machines for different industry applications. These modular machines allow manufacturers to configure machines based on certain production requirements. Also, multiple operations in a single cycle will be implemented to limit the need for further equipment in operation by these machines. Immensely useful for truly flexible power press machines able to work different materials, including advanced alloys, and composites for the automotive, aerospace, and electronics industries.
Conclusion
The future of power press machines in metal processing, to a great extent, will depend on developments in technology with emphasis on automation, efficiency, and safety. Integrated CNC control, IoT connectivity, energy savings, and smart safety will revolutionize the field of manufacturing. As the world changes over to smart factories and sustainable production, it becomes obligatory to invest in upgrades for power press machines to keep pace with the market trend in evolving competitivity. Smartness, speed, and adaptivity will usher power press machines into the next chapter of metal-fabrication innovation in years to come.
Leave a Reply