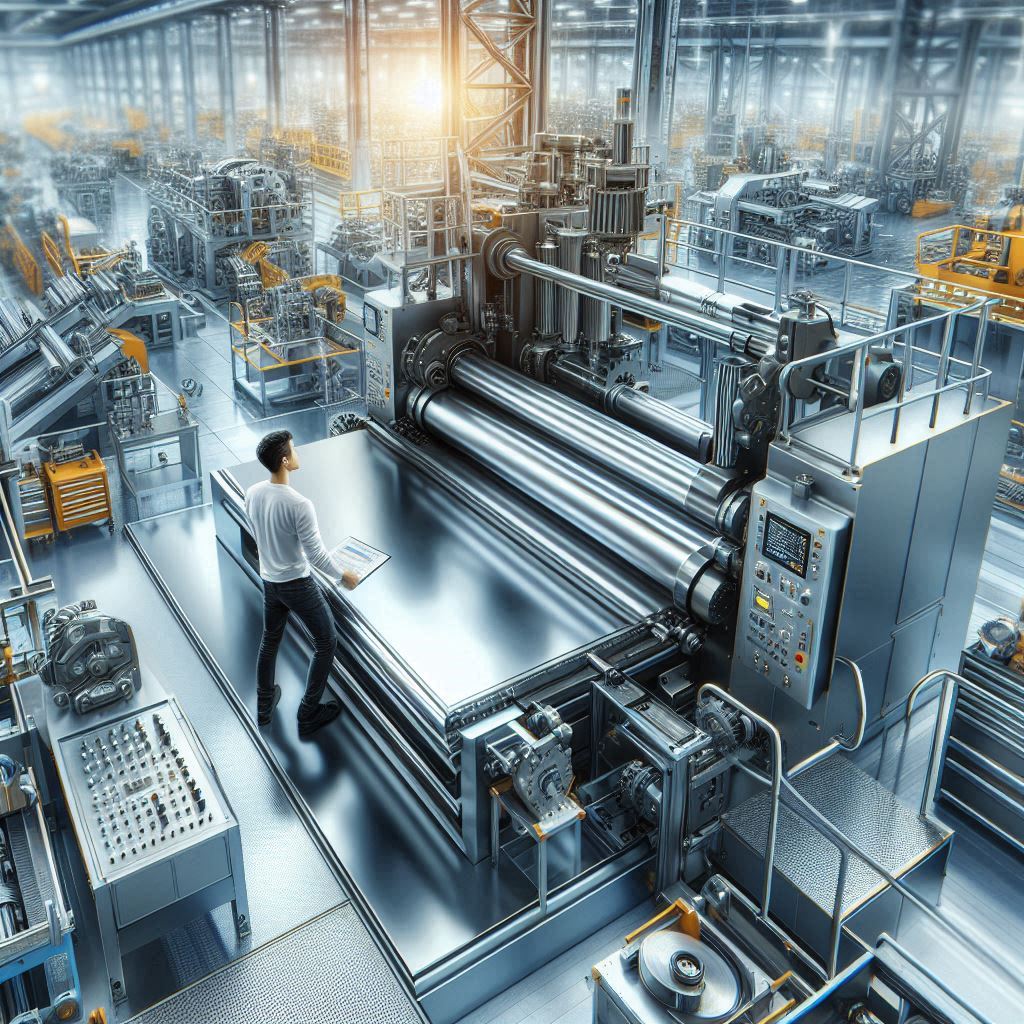
The changing metalworking shop and industry continue to evolve throughout the years while modern technologies enhance production processes, increase safety levels, and maximize overall efficiency. Among the major breakthroughs in the field is the advent of automatic plate rolling machines, which are redefining how metal plates are shaped and formed and providing unrivaled levels of precision and efficiency. This article discusses the role in which automatic plate rolling machines enhance the accuracy of the fabrication process of metals and at the same time raise the productivity levels of manufacturing operations.
What do you consider an Automatic Plate-Rolling Machine?
Heavy-duty machines for rolling and shaping large metal plates into cylindrical, conical, or any curved shape are called automatic plate-rolling machines. Automatic plate rolling machines are fully automated and work independently from manual methods. These machines consist of advanced technology, including various digital systems for control, advanced sensors, and computer software that carries out control of the entire rolling process. The operator is able to input certain parameters, for example, thickness, diameter, curvature, and such characteristics, whereas the machine automatically takes over and adjusts according to produce the right shape with minimum human interaction.
Enhancing Precision in Metalworking
Metalworking requires great precision, especially when the parts are mass-produced and require high uniformity. Automatic plate rolling machines are designed to provide consistent results brought about by the reduction of human-dependent errors and variations in the final product. A digital interface allows the operator to input exact specifications for roll tolerances, ensuring the machine maintains tight tolerances throughout.
For instance, the machine can apply a variable pressure and rolling speed to its plate depending on the material thickness and curve. Such a measure guarantees some precision in rolling conditions so that the resulting product does not deviate much from the prescribed tolerances.
Advanced Feedback Systems
Automatic plate rolling machines very often have built-in feedback systems that monitor the forming process continuously. They are equipped with sensors that track the behavior of the material during the rolling operation and adjust the machine’s parameters accordingly in real-time in case of any disturbances. The machine will instantly change its parameter settings when abnormal activities are detected by its feedback systems, such as excessive elongation or a curve deviation, thus ensuring precision for the entire production run.
Reducing Material Wastage
Most importantly, increased precision results in lowered material wastage. Excessive rolling leads to errors such as wrinkling and dents, and such defects call for scrap. With automatic machinery, the component manufacturing process is precise; therefore, the first shaping will be the correct one for minor deviations and material waste.
Conclusion
The advent of Automatic Plate Rolling Machine is a revolution to the metalworking world. They are almost essential for the modern manufacturing process due to the enhancement of precision and efficiency. These machines use consistency and accuracy to promote maximum efficiency, minimize materials wastage, and generate fast production turnaround times-perhaps significantly impacting various manufacturers’ profitability in different industries. With advancements being made in technology, it is anticipated that even more advanced plate rolling machines will be introduced into the market to drastically redefine precision and efficiency in the metalworking environment.
Leave a Reply